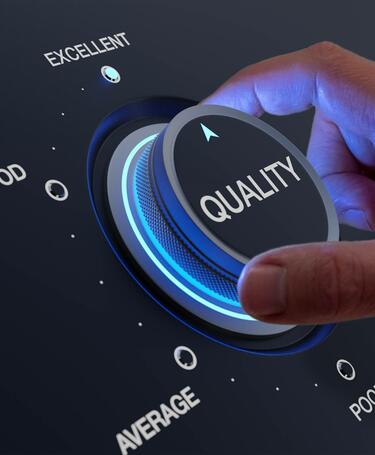
Exploring hidden dimensions: quality culture and cultural quality – Part 2
Progress indicator
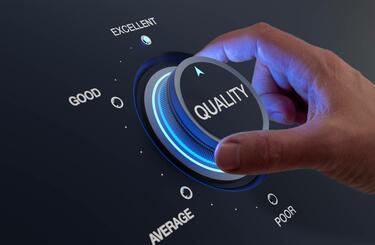
Continuing their series, IRCA-Certified associate auditor and international project quality lead Rasoul Aivazi and retired auditor Richard Brett use stories from their own experiences to explore how Japanese philosophies are intrinsic in quality.
Aivazi is an International Project Quality Lead and a committee member of the CQI Audit SIG, while Brett, now retired, previously had roles as Japan Quality SME and Audit Manager for GSK and is currently Vice-Chair of the Audit SIG.
The quality of products and services in Japan is deeply rooted in its culture, often unconsciously absorbed without direct awareness.
The unconscious cultural influence on quality in Japan is a potent force that shapes products, services, and professional environments. Central concepts like Monozukuri (the craftsmanship spirit), Kaizen (ongoing enhancement and continual improvement), and Kodawari (relentless focus on detail) underscore this relationship.
In Part 1 of this series, we offered three quality stories we had personally experienced. In this second part, the stories continue.
Personal Experiences of Cultural Quality
Story 4: Quality and non-quality
I was visiting our company’s Japanese facility to agree quality standards for products manufactured in Europe and for sale in Japan. For statistical sampling in Europe and America, we use Acceptable Quality Levels (AQLs) to determine pass/fail criteria.
During our first meeting, it soon became clear to me that this discussion was not going well.
When I asked my Japanese colleagues what their concerns were, I was told: "We don’t use AQLs here. If you have acceptable quality levels, does that mean you have acceptable levels of non-quality? Our customers would not be happy with that".
I realised that the terminology was highly significant and that we needed to find a different way of defining quality. We talked about what factors were important and what were essential. I then suggested that we use the terms 'critical quality' and 'critical quality attribute' to define what was acceptable and what was not.
Once we moved away from the concept of a level of non-quality as acceptable, we were able to agree on appropriate quality standards.
This showed me the importance of understanding the local culture and sensitivities about the language we use.
Story 5: Customer Complaints
In the West, we say "The customer is king". I was told by a Japanese quality manager that "the customer is God – and customer complaints are the voice of God".
In Japan, the customer is always right – even if the problem was because the customer did not use the product correctly. If the customer can misuse the product – if it is not error-proof – then it was not properly designed, and poor design is poor quality. It is no good trying to point out that the product has a 99.9% customer satisfaction rate For the dissatisfied customer, the product he has bought has a 100% failure rate and this is all that matters.
It is therefore essential to respond quickly to the customer, acknowledging the complaint, and apologising for the defect and the poor service he has received. This must be followed up by a comprehensive investigation, including a root cause analysis, and an effective corrective and preventive action plan. It may not be (and often it is not) possible to achieve zero defects, but in Japanese quality, this is always the vision.
Designing out failure modes is essential for the manufacturer and every complaint, whether 'justified' or not, should be seen as an opportunity to improve.
The Unconscious Cultural Influence on Quality in Japan
The above stories, both relevant to quality management, are just examples of several Japanese cultural influences in quality.
The three central concepts of Monozukuri, Kaizen, and Kodawari serve as a starting point. However, we also want to delve deeper, examining ten dimensions of how culture shapes quality in Japan.
The ten concepts of:
- Monozukuri
- Kaizen
- Kodawari
- Wa and Chouwa
- Keigo and Giri
- Gaman and Nintai
- Dai-ichi inshou
- Dandori hachibu
- Omotenashi
- Hōsō
are deeply entrenched in the Japanese psyche and contribute significantly to the country's reputation for quality.
The ten concepts are literally translated into:
- spirit of manufacturing, which represents the cultural pride of craftsmanship;
- continuous, incremental improvements;
- obsession with detail;
- collaboration and harmony;
- hierarchy and tradition;
- patience and persistence;
- utilising the first impressions;
- importance of preparation/pre-planning;
- hospitality and service;
- packaging and wrapping.
When embraced and harnessed effectively, these cultural influences can become catalysts for professional success.
In understanding these unique cultural influences, professionals in Japan and those interacting with Japanese organisations can better navigate the working landscape.
These cultural elements not only enrich the professional environment but also play a significant role in the creation and delivery of the quality services and products for which Japan is renowned.
Ford Motor Company story:
We began Part 1 of this series with a story from the Ford Motor Company. It continues here:
In pursuit of an answer to the question of why consumers preferred Japanese-made transmissions, Ford Motor Company finally decided to dismantle the two different transmissions for an in-depth comparison.
The American-made car parts were all within specified tolerance levels. However, the Japanese car parts were virtually identical to each other, and much closer to the nominal values for the parts - e.g., if a part was supposed to be 1ft long, plus or minus 1/8 of an inch (300 mm ± 3mm) - then the Japanese parts were all within 1⁄16 of an inch (1.6 mm), less variation (300 mm ± 1.6mm). This made the Japanese cars run more smoothly and customers experienced fewer problems.
At its core, this exploration reveals that the unconscious cultural influence on quality in Japan is not simply about meeting standards or exceeding benchmarks; it is about a deeply ingrained ethos that permeates all aspects of life.
As such, professional success in Japan is not merely about proficiency in a given field. It involves embracing a culture of quality that requires a deep understanding of these cultural influences and integrating them into one's professional life.
This discussion will continue in Part 3 of this series, exploring hidden dimensions of national aspects when you work in Japan: catalyst for quality culture.
Don't miss Part 1 of this series
Read more on the theme of the hidden dimensions of quality culture and cultural quality in the first part of this series by Rasoul Aivazi and Richard Brett
Quality World
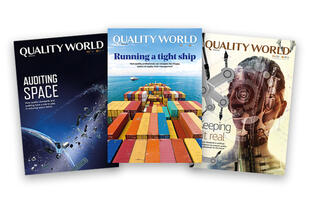
Get the latest news, interviews and features on quality in our industry leading magazine.