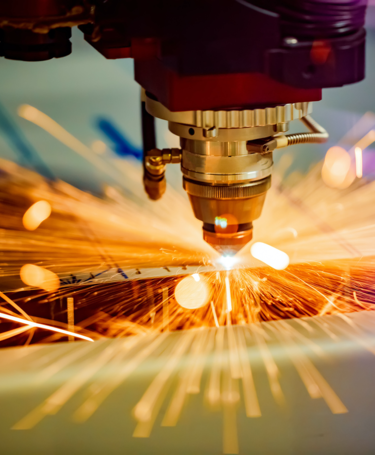
Improving product reliability in manufacturing
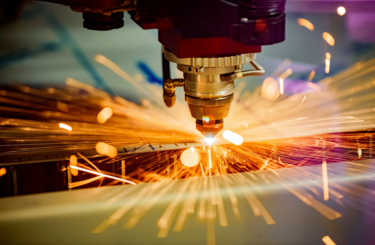
Dr Louis Redding, CQP FCQI, discusses some useful methods to help improve complex engineering products.
Manufacturers of complex engineering products such as aero-engines, gas turbines, and high value medical machines (scanners), continue to seek innovative business and operations strategies in order to maintain and improve their competitive positions. These initiatives are driven by the pressures of limited and diminishing resources, the increased demand for products from emergent economies, and increasingly stringent legislation by regulatory bodies (eg nuclear, aviation, automotive, mineral extraction, and oil and gas), which originate from such global markets within these sectors.
Evidence documented in peer reviewed academic research relative to Product Service Systems (PSS) and through-life engineering services (TES), suggests that these pressures could mean that manufacturing organisations are no longer able to compete on cost alone.
Strategies
In response to this, two strategic approaches have emerged and continue to develop at a rapid rate.
PSS originated in Scandinavia and are a response to the realisation that sustainable solutions are required in consideration of environmental issues and the recognition that the planet’s resources are limited. These business strategies relate to how the organisation seeks to acquire its revenue and document organisational evolution which moves from the supply of product, through:
- product oriented;
- use oriented;
- result oriented phases, to that of the main service provider.
Servitization, however, is an alternative response to these pressures. This process sees manufacturers adding increasing levels of service integration to their offerings by increasing their competitive advantage and protecting their competitive space. The author suggests that servitiszation is the process through which PSS business strategies evolve. A typical example cited in the literature is the business strategy which has evolved and is observed in Xerox Plc. From the starting point of being a manufacturer of photocopiers and scanning equipment sold on a traditional transactional basis, they have evolved to the point that they gain the majority of their revenue from selling fully integrated printing solutions.
Users of their products now purchase the number of copies made of documents and files and do not purchase the machines. Xerox own and lease their products to the user and gain additional revenues from their continued use, routine maintenance activities, and sale of consumables. Their installed machines can be connected to their servers which monitor asset performance, thereby facilitating online billing, supply of consumables when needed, and maintenance when degraded performance is detected. Put simply, they take ownership of all their customers’ printing requirements by offering fully integrated solutions.
The adoption of either (or both) strategies sees ‘whole life’ value-added propositions emerging for stakeholders. This, in turn, provides revenue streams to the manufacturer throughout all phases of the product lifecycle via enhanced service support and availability contracts.
While such strategies establish ongoing revenue streams for the manufacturer throughout the product’s lifeline for use, they also involve the transfer of risk to these revenues from the user to the manufacturer. These risks relate to loss of revenue resulting from degrading and/or failing products. This exposure to revenue risk for the manufacturer has seen the reliability and the quality of the performance of the product and service offering becoming ever more central to the manufacturers’ operational performance.
Organisations have sought to mitigate this risk by adopting proactive reliability engineering methods, delivered by condition-based management techniques. Through-life engineering services (TES) are adopted as an integral part of their business and operations strategies. The author says that TES can be defined as: "The application of existing and emergent product and/or system monitoring, diagnostic, and prognostic technologies, supported by state-of-the-art maintenance, repair and overhaul practices, methodologies, and strategies, informed by advanced reliability and quality tools which seek to mitigate risk to the product’s or system’s availability to deliver a product’s (or system’s) design intent, whilst offering a sustainable solution at minimum whole lifecycle cost".
Central to mitigating these risks is the ability to understand how the product is performing when in use. Within high-value complex engineering products any degradation in the product’s ability to deliver its design intent (degradation of function) is detected through the use of condition-based monitoring and management techniques. Well-documented integrated vehicle health management (IVHM), and prognostic health management (PHM) systems are examples of such product management strategies.
Guidance for manufacturers
The foundation for effective, stable, and repeatable product support strategies is effective governance. This is achieved by bespoke standards, procedures, guidance notes and codes of practice relating to the subject matter under study. However, when searching for such governance relative to TES, such guidance proves to be elusive. Of that which does exist, it is observed that it relates to either: ISO 55000:2014 Asset management — Overview, principles and terminology, or the supporting constituent elements of TES, which includes: sensors, system architectures, coding techniques, and non-destructive testing methods – thermography, x-rays and ultrasounds – and not to TES directly.
In order to start addressing these issues, the British Standards Institute (BSI) has been collaborating with Cranfield University’s Through-life Engineering Services Centre, industrialists with an interest in the field, and academics from leading universities to investigate the scope and content of TES, and to develop aligned governance and frameworks.
In addition, this collaboration between Cranfield University and other stakeholders has seen the launch of the National Strategy for Through-life Engineering Services (2016) entitled: Delivering Economic Growth: Making Things Work Better for Longer. Within this document, three priority areas for action are identified. These are:
- The creation of a cross sector UK National TES centre of excellence/Council with industry.
- Government departments should change their procurement policy by putting emphasis on through-life costs.
- A new government policy framework for Intellectual Property Rights (IPR) sharing should be developed, with open book services and a technology framework which covers IPR law and improves protection.
The author suggests that these areas relating to TES can provide major opportunities for manufacturers such as:
- A bespoke ISO Standard for TES which could offer manufacturing organisations accreditation when following strategic PSS business models.
- Defining the links and distinctions between any emergent TES standard and current guidance (Typically ISO 9000 Series, and ISO 55000 Series standards).
- Defining and linking a standard for TES with the current published guidance [PAS 280:2018 –Through-life engineering services].
- A greater understanding and awareness of, and the delivery of, standards and guidance notes which explicitly relate to business model innovation for manufacturing organisations who seek to adopt PSS and Servitized business models underpinned by TES generic solutions.
- Increased understanding of the frameworks and definitions of cost models – and associated risk modelling – for organisations seeking to compete through the adoption of extended availability contracts (Typically 20 years plus for high value products).
The challenges, when solved, offer a significant gain for stakeholders as ‘first past the post’ will define the governance and terms of accreditation to any emergent standard for the manufacturing sector.