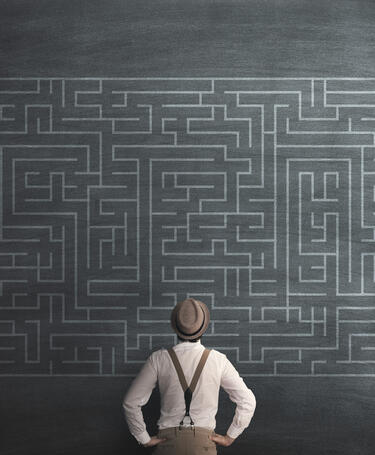
Sustaining stakeholder buy-in – Part 2
Progress indicator
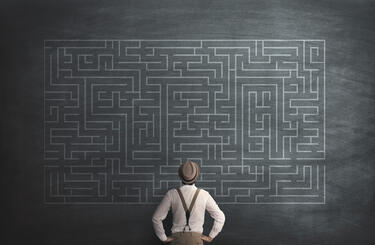
In the follow-up to our two-part series on sustaining stakeholder buy-in, Professor Mitter Vedu, CQP FCQI examines the utility of the Constraint Management, Six Sigma, and Lean methodology in sustaining continued involvement and support from stakeholders and participants.
Many enterprises that start up begin as a one-man show, with the owner-manager and his/her close team putting into practice their accumulated business acumen and knowledge base with an uncommon dedication. As success knocks at their door and the business grows, more and more people join, and the growth pangs begin to manifest. Among the many new systems required to ensure repeat performance so as to retain customers, the absence of a continuous improvement infrastructure shows up as a major weakness. Many approaches get examined as though each one of them can be a panacea or quick fix for all their ills.
Among the approaches are:
- Total quality management;
- Business process reengineering;
- Six Sigma;
- Benchmarking;
- Lean (and Kaizen);
- Theory of constraints;
- Business excellence.
The consultants, who are called in, add to the confusion by claiming their methodology is the be-all and end-all of the quality management structure required. The organisation tries out one after another, gets disillusioned by the results over time, and turns to another ‘flavour of the month’. The situation turns out to be like the story of five blind men ‘seeing’ an elephant with their other senses in different ways, which leads to discord and consequent resistance to any change.
Seven layers of resistance to any problem-solving or process improvement effort manifest as follow:
- Agreeing that there is a problem.
- Agreeing on the problem.
- Agreeing on the direction of the solution.
- Agreeing that the solution will solve the problem.
- Agreeing that the solution will not lead to significant negative side effects.
- Agreeing on the way to overcome any obstacles that may appear when implementing the solution.
- Agreeing to implement the solution.
Many a change effort falls by the wayside as the leadership fights ‘fires’ and rewards the crisis-managers, much to the chagrin of those who aim to work on the root causes. Problems claimed to have been solved keep repeating, with no end in sight.
For those who can ‘see’, it becomes obvious that a ‘burning platform’ is required to get the skeptics to fall in line. Can crises be turned into the ‘burning platforms’? The riddle needs a shrewd look.
Amongst the improvement approaches listed above, three have strong potential to solve this riddle. They are Lean, Six Sigma and Theory of Constraints (Constraints Management). The question arises as to how they should be adopted or sequenced to obtain the best results through active stakeholder engagement.
Let us examine how each of these differs in their basic characteristic.
Constraints usually create a crisis situation and get the attention of most people at different levels, as output is in sudden jeopardy, whereas Six Sigma and Lean in standalone mode require education, understanding, and conviction regarding their long-term benefits for commitment.
A constraint is a problem to productivity in some form and triggers a cost impact of some kind. Therefore it gets management attention. It appears highly expedient to create a ‘burning platform’ around a constraint. The resolution of the problem(s) posed by constraint, besides quick fixes, requires an approach to remove the constraint by one of three approaches to remedy the root cause:
- Manage overall throughput to reduce constraint in cases of capacity inadequacy.
- Enhance first pass yield in case of a surfeit of rework.
- Minimise inventory in case of wasteful practices.
Table 1, below, shows the different emphasis in a five-step process between Constraint Management, Six Sigma, and Lean practices.
Process |
Step 1 |
Step 2 |
Step 3 |
Step 4 |
Step 5 |
Total Focus |
Constraint Management |
5 |
3 |
17 |
4 |
1 |
TCT* 30 days Step 3 |
Six Sigma |
500 |
300 |
170 |
4,000 |
100 |
DPMO* Step 4 |
Lean |
50 |
170 |
30 |
40 |
10 |
WIP* Step 2 |
Table 1
*(TCT = Total Cycle Time; DPMO = Defects Per Million Opportunities; WIP = Work In Process.)
Constraint Management focuses on cycle time (Step 3); Six Sigma focuses on DPMO (Step 4) and Lean focuses on WIP (Step 2). Lack of integration between the approaches results in dispersed efforts and confusion in the allegiance to the improvement process.
A preferable approach, therefore, could be to have an overall goal for Total Cycle Time (TCT) of ‘x’ subserved by a DPMO goal of ‘y’ and a WIP goal of ‘z’. In the case of Table 1 process, it could be x=3days; y=100 and z=10 all at the end of Step 5 and work on constraints successively to achieve it. The effects of such an improvement in overall productivity can be projected to the process owner/sponsor of the continuous improvement programme, as a convincing argument for the commitment of resources and support.
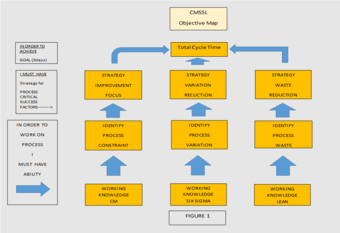
Figure 1
Figure 1, above, puts in perspective the Constraint Management, Six Sigma, and Lean (CMSSL) Objective Map. Firstly, there is a need to spread working knowledge of the three disciplines (Constraint Management (CM), Six Sigma, and Lean) among employees. They do not have to be experts; just-in-time training can be imparted during specific projects for improvement. CM enables them to identify constraints; Lean to identify wastes; and Six Sigma to identify variation. These are necessary conditions for improvement project teams to engage in problem-solving and improvement. Once the top constraint is taken up for problem-solving/improvement, the strategies of variation reduction, waste reduction and improvement focus are deployed, as they are the critical success factors for the success of the improvement effort. The overarching objective of the effort shall be to reduce Total Cycle Time (TCT) at each constraint successfully. Referring to Table 1, the ultimate objective could be to reduce TCT to three days, for example.
The path to excellence through continual improvement requires an amalgamation of the three disciplines in an optimum sequence. Let us briefly understand each in this context before trying to amalgamate them in the context of an identified constraint.
Firstly, Constraint Management is approached as follows in Figure 2.
CONSTRAINTS MANAGEMENT |
---|
Identify the system constraint (item limiting system performance). |
Decide how to exploit system constraint (maximise throughput at constraint). |
Subordinate everything else to the system constraint. |
If necessary, elevate the system constraint (increase capacity to market demand) or else remove constraint by other means. |
Start again with next constraint. |
Six Sigma is typically approached as in Figure 3, below.
SIX SIGMA (DMAIC) |
---|
• Determine process entitlement at chosen process (find distribution of values around specs and see sigma when centered). |
• Work to improve process capability to remove constraint (if entitlement adequate work to center the distribution w.r.t specs) (else work for improvement in spread). |
• Sustain the improvement (standard operating procedures) |
• Move to the next constraint to first pass yield. |
Lean is approached typically as in Figure 4.
LEAN |
---|
• Important steps in process capable. |
• Practice just-in-time, insist on suppliers to do similarly. |
• Reduce inventory. |
• Reduce cycle time. |
• Reduce cost. |
• Improve quality. |
• Be more competitive. |
The integration of the above three approaches has to be based on the logic that the identified constraint must be permanently removed by variation reduction, followed by waste reduction and consequent streamlining of operations. It is well known that in business settings elimination of one constraint exposes another constraint and so on, until complete streamlining of the system is achieved. It is like the proverbial ball under the carpet which moves from one place to another until the root cause (the ball) is removed. The best approach, therefore, would be to take up one constraint after another, and seek optimisation through firstly variation reduction, followed by Lean practices. It is common knowledge that, unless defects are reduced, work-in-process inventory cannot be optimised.
Figure 5 lists out the sequence incorporating the CMSSL approach.
CMSSL |
---|
• Find the most important constraint to productivity. |
• Exploit the constraint by subordinating other processes to it using Six Sigma and Lean in sequence. |
• Move to the next most important constraint and do likewise and so on. |
• Apply CMSSL to all processes. |
• Reap the benefits and sustain. |
By following the above cycle, it is possible, as I have seen in quite a few cases, to achieve the following results, to a considerable extent, as in Figure 6.
RESULTS |
---|
• Commitment from senior leadership. |
• An effective process for managing change in an ever-changing environment. |
• Complete involvement of the relevant workforce. |
• A robust design for a new business change management process. |
• A ‘burning platform’ for energetic change and a captive audience that is ready for change. |
• Total management commitment to a process of ongoing improvement. |
The CMSSL method is a desirable way for quality professionals to participate in, not as advisers or evangelists, but as assurance people taking the lead as facilitators, leaders or enablers. By using the ‘burning platform’ philosophy, quality professionals can attract the attention and sustained buy-in of all concerned for a fruitful cooperation to achieving a tangible and durable result in every improvement project. Thus the quality professional turns into a desirable assurance member among employees and process owners alike. The existence of a quality management system, according to ISO 9001:2015, is a favourable factor for such an approach from a knowledge management perspective to retain the benefit accruing from such effort.
About the author: Professor Mitter Vedu FCQI has more than 50 years experience in strategic quality, in Switzerland and India. He is a Six Sigma Master Black Belt.
Read it!
Professor Mitter Vedu, FCQI, examines the approach to sustain stakeholders’ interest in continuous improvement methodologies in the first article of this two-part series
Quality World
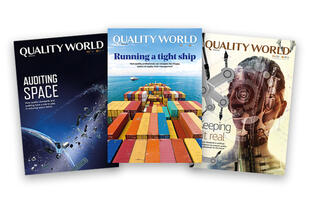
Get the latest news, interviews and features on quality in our industry leading magazine.