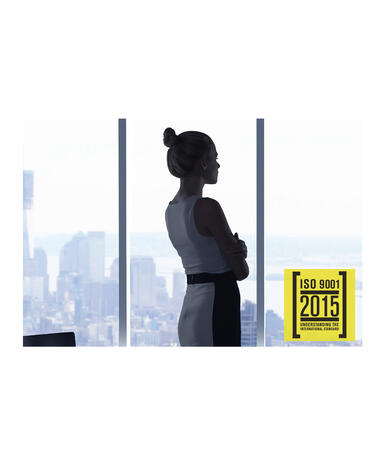
Leadership and commitment in ISO 9001:2015
Progress indicator
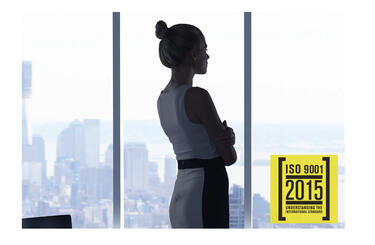
Alexander Woods, CQI certification manager, explains why the theme of leadership is so crucial in the revised quality management system standard.
Of the revisions to ISO 9001, Clause 5 – leadership and commitment, is arguably one of the more hotly debated topics. But what are these changes and why are they proving such a focal point of discussion?
Clause 5 requires that top management demonstrate that it actively engages in and undertakes key quality management system activities. It is no longer sufficient for them to simply ensure these activities occur. This means top management must get actively involved in the operation of their QMS and quality should become embedded in routine business operations and not a separate and discrete activity. This approach is reinforced by the demise of the role of ‘management representative’ in the standard.
So, to whom are we referring when we use the term ‘top management’? Annex SL provides us with the following definition:
“(the) person or group of people who directs and controls an organisation at the highest level.”
It does not mean the management representative, it does not mean the quality manager, it means the person at the very highest level of an organisation. It is worth noting that if the scope of the QMS covers only part of an organisation then ‘top management’ refers to those at the highest level of that part only.
Let us use as an example a company with a head office in Manchester and manufacturing plants in Cumbria, Lancashire and Yorkshire. If the scope of the QMS encompasses the entire company – head office, manufacturing et al – then ‘top management’ refers to the CEO of that company.
Should the scope of the QMS only cover the manufacturing function, then the it refers to whoever is at the highest level of that part of the organisation – the manufacturing director, or similar.
If the QMS covers the Yorkshire plant alone then ‘top management’ is the managing director of that site. The revised standard identifies specific aspects of the QMS where top management is expected to demonstrate both leadership and commitment. This includes a number of activities which top management must ensure happen, such as:
- The establishment of a quality policy and quality objectives which are compatible with the context and strategic direction of the organisation
- The integration of the QMS into the organisation’s business processes
- The availability of resources needed for the QMS and that the QMS achieves what it is meant to achieve.
These are all activities which top management must ensure get done, but they do not necessarily have to do them themselves. More importantly are the following activities, which top management cannot delegate or assign elsewhere, but must undertake themselves:
- Taking accountability for the QMS
- Promoting the use of the process approach and of risk-based thinking
- Communicating the importance of the effective QMS and of conforming to the QMS requirements
- Engaging, directing and supporting persons to contribute to the effectiveness of the QMS
- Promoting improvement
- Supporting other management roles in demonstrating their leadership.
Business leaders will face scrutiny
Not only is top management going to have to undertake these activities but they are going to be audited, and so must also provide evidence that they have done so. Business leaders will face scrutiny from within their own organisation through internal audit, as well as from second and third party auditors.
For some organisations and corporate cultures, this is going to require a significant shift in thinking. For the internal auditor, the prospect of inspecting the commitment of their employer to QMS will be daunting, understandably so. Auditors are going to have to approach these interactions with tact and diplomacy. More importantly, auditors will have to “speak business”. They are going to have to describe their activities and intentions in terms that their boss will understand – remember, for all that adopting a QMS has always been a strategic decision, many business leaders will not be familiar with the language and theory ISO 9001.
While some may decry that CEOs will never subject themselves to audit, that they don’t have the time to get involved in the nitty-gritty, day to day operation of their QMS, if they want to retain their certification that’s exactly what they are going to have to do.
The challenges are evident. But so too are the opportunities. Quality professionals have a body of work to do to get the buy-in of top management. For all the role of management representative is no longer a requirement of the standard, if it is a useful function for the organisation then it should absolutely be retained. One could even argue that management representatives have an even greater role and responsibility now in preparing the organisation and top management for transition while maintaining the integrity of any existing QMS.
Where top management is already actively involved in the QMS and understands the context of what it is expected to achieve this will be relatively easy.
A body of work to be done
But in organisations where top management is not engaged, and perhaps not at all familiar with the concepts and language of ISO 9001:2015, there is a body of work to be done in educating and informing top management about ISO 9001 management systems, their purpose, their language and their benefits.
This can often come down to the bottom line – how much money is this going to save and/or make me? But the opportunities are greater than that. The opportunity for cost savings from integrating, for example, quality, environmental and occupational health and safety management systems with each other is there, as it is from embedding quality within existing business management systems, processes and procedures.
Ultimately, a QMS is designed to support a business to improve and deliver the products and/or services its customers require, to their satisfaction, consistently, effectively and efficiently. And what business leader doesn’t want to do that?
Member only
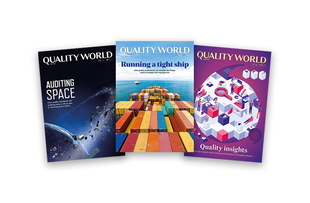
This article is free to access for a limited time only. Only CQI and IRCA members receive access to all content.
Get the latest ISO reports and resources
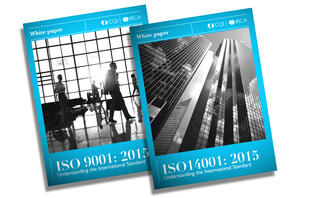
Our many reports and resources will help you achieve a smooth transition to ISO 9001:2015 and ISO 14001:2015.