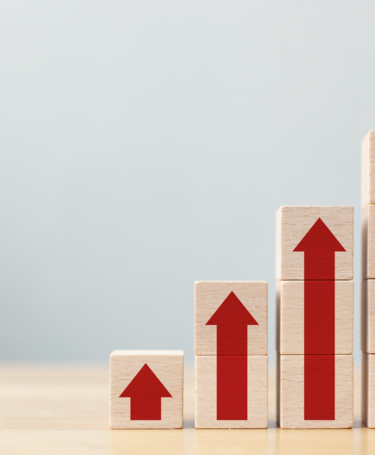
Applying the Deming System of Profound Knowledge

Christopher Chinapoo, Managing Director at Five Star Quality and Justice Associates in Trinidad, explains how Deming’s management principles can be applied to improve business supply chains.
The first duty of a sound business is to create a customer, stay in business and grow sustainably. The customer is the most important element of product or service delivery. The customer determines value throughout their total experience of product or service. One of the most fundamental points about the Deming Management method or System of Profound Knowledge (SoPK) as it’s otherwise known, is that it is about changing the way we think about quality management systems (QMS) and their interactions. Dr Deming’s principles are focused on thinking together, learning together, working together and improving together. He insisted that the four components of the SoPK cannot be separated because they all interact with each other.
As with Deming’s 14 points, no single point stands alone. He described, for example, how knowledge of psychology is incomplete without knowledge of variation, just as understanding of variation will be incomplete without appreciation for a system. Many continue to separate or give inadequate consideration to all components. When taken apart, essential properties are lost as well as the value created from the interaction. If separated, the four components of a system of profound knowledge are incomplete.
The four components include:
- Appreciation for a system
- Theory of knowledge
- Psychology
- Understanding variation.
Deming proposes that the aim of the system is to ensure everybody wins. He emphasises forming meaningful, long-term mutually beneficial collaboration with customers and suppliers – relationships that allow for both to be part of the system beyond mere transactional considerations.
Understanding that the system is not the sum of its parts, but the result of interactions. This expands the definition of customers and also sets expectations to achieve customer delight, as opposed to merely meeting specifications, requirements and satisfaction. It is important to recognise that the system should be designed with the organisation’s future in mind.
Understanding system dynamics from the lens of the System of Profound Knowledge provides deeper insights and allows staff within an organisation to develop a transformatory view of how the system should operate for their customers and supply chain. SoPK helps give an immediate appreciation that systems extend beyond processes and activities and includes the future, the customers and extends to all boundaries and interactions.
Appreciation for a system
Management of a system in which company’s deliver their products and services, requires knowledge of the interrelationships between processes, sub processes within the system and everybody that works and interacts with it. Deming stresses that “the system must be stated by management. Without an aim, there is no system.” All 14 points support optimisation of systems and processes.
However, the following points, in theopinion of the author, helps to characterise Deming’s thinking about systems and improvement:
- Point 1 - Create constancy of purpose
- Point 2 – Adopt a new philosophy
- Point 4 – End practice of awarding business on price tag
- Point 5 – Improve constantly
- Point 9 – Breakdown barriers to communication and cooperation
- Point 11a – Eliminate work standards on the factory floor
- Point 11b – Eliminate management by objectives
These points emphasise the importance of appreciation of the system.
Knowledge of variation
Profound knowledge helps leaders remain mindful that there is always variation acting on the system. It is important to understand the type of variation before taking actions that lead to suboptimisation of the system.
Common causes of variation come from within the process. They generate outcomes that are different, but not significantly different. Special causes intervene from outside the process and produce outcomes that are significantly different. It is crucial for all leaders to understand how to avoid mistaking common causes for special causes and vice versa.
Making this distinction is critical for managers in determining an appropriate improvement strategy for their businesses. For common cause variation, the appropriate strategy is to change and improve the process. For non-random and special cause variation, the appropriate action is to find, remove and prevent the recurrence of the special cause. No amount of work on a process will address a special cause because uncontrolled variation comes from outside of the process.
Taking action on variation is not the same as attempting to simply conform to requirements or bring management systems within the control limits and specifications. Again, all 14 points can be explained from the perspective of knowledge of variation.
Theory of knowledge
The third component of profound knowledge promotes learning as individuals and as an organisation. Operational definitions and the application of plan, do, study, act (PDSA) control charts are all tools, designed to help us better communicate, think, work, learn, innovate and improve together. The tools are not a substitute for the thinking required to apply profound knowledge.
One of the best methods to explain the theory is to conduct the ‘red beads’ experiment, which provides insights and appreciation of a system and knowledge of theory of variation. Beyond that, however, the bead experiment demonstrates the effects of the ‘forces of destruction’, which lead to suboptimisation of the system, robs workers of joy and pride in workmanship and so on.
Knowledge of psychology
Psychology helps us to understand people, interaction between people and circumstances, interaction between a manager and his/her team and any management system. Managing these interactions of human emotions and the system is a critical contribution to the SoPK. Several points emphasise the importance of knowledge. Points eight (drive out fear), 10 (eliminate slogans, exhortations and targets), and 12 (remove barriers that rob people in management and engineering of their pride of workmanship; this means abolishment of the annual merit rating and of management by objectives) all elevate the importance of psychology in managing organisational transformation.
Profound differences in the Deming management method
Many of Deming’s ideas seem commonplace and are in fact incorporated in a number of the recommended ‘best practices’. However, they are not the same. The system of profound knowledge may use the same words, but, it is profoundly different in the way it emphasises:
- Studying the theory of the system and with it continually learning, innovating and improving continually using the new lens of the SoPK to explain why the system works or does not work.
- Managing the company as a system and optimisation of the whole, as opposed to optimising parts of the former.
- The obligation of any component of a system is not to maximise its own production, profit, sales or other competitive measure. To optimise some components may operate at loss to themselves to ensure everyone wins.
- Cooperation and warns against fostering competition in all its forms. Emphasising cooperation with competitors to expand the market, as opposed to simply seeking increased market share.
- Intrinsic motivation as opposed to extrinsic motivations.
- Promoting pride in workmanship as opposed to over justification.
- Actively working with suppliers, customers and competitors to improve and innovate. Going beyond superficial relationships and establishing the need to manage variables beyond the typical boundaries of a company.
- Abolishing performance evaluation, rankings and merit systems.
- Focus on the process causing results and not judging results.
- Consideration of unknown and uncountable variables. Deming suggests that companies should stop managing using visible figures alone.
- Understanding and improving systems within the capability of the system and avoiding over-reliance on setting numerical goals and targets with little or no consideration to variation.
- Estimating the total cost of use of materials or service. Considering purchase price and predicted cost of problems of use of them and the effect on quality of final products.
- Quality in design and planning and not inspection.
- Learning over evaluation, and explanation over analysis as the foundations for improvement.
The mindset practices associated with Deming are not about command and control, fear or manipulation and are in direct contradiction to much of what is taught and practiced by management consultants and leaders.
Incorporating a thorough understanding of Deming’s management method will help companies apply his principles and improve their business processes effectively.