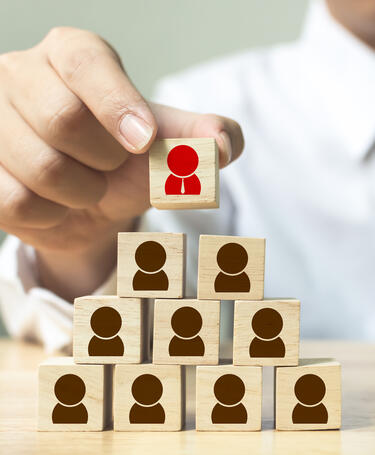
How to structure your quality team
Progress indicator
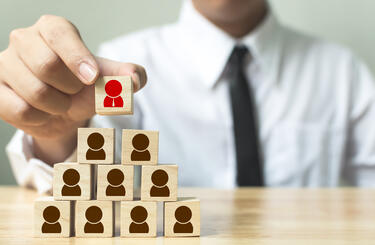
Kate Armitage, Head of Quality Assurance at Qualsys, puts together her best practice guide for who you should include in your quality team.
Long gone are the days when all your quality team was expected to do was tick a long list of regulatory compliance checkboxes.
Modern quality management teams are accountable for delivering a balanced scorecard of metrics – from improving efficiency to increasing profitability and waste reduction initiatives to enabling growth.
Despite all this responsibility, quality teams rarely scale at the same pace as the rest of the organisation. In fact, the Global Governance, Risk and Compliance Report 2019 confirmed this. For example, in the past twelve months, 48 per cent of quality professionals said that the business had grown, but only 20 per cent said their department had increased in size.
Growing a quality team is, unfortunately, still seen as a non-value added overhead, rather than an investment for the future that will have a direct impact on the bottom line.
Teams must be structured in a way to meet targets. What that structure looks like can hugely impact your results as a business and a department. While there is no ‘one size fits all’ approach to follow when structuring your quality team, there are some best practices I’ve seen work well in organisations, and they tend to align with the size and stage of growth of your business.
I’ve put together my best practice guide for how many people you should have in your quality team and what the structure of your team should look like.
Small businesses
For regulated organisations, such as those in the life science, clinical trials or consumables sector, there is a requirement for a dedicated quality manager from the day the business is launched to avoid retrospective validation and compliance issues.
However, for most other small businesses or a start-up, your quality team is probably just zero to two full-time employees. Your quality manager is probably wearing many hats – health and safety, environment, information security, risk, training requirements, documentation control, etc.
At this stage in your organisation’s life, you are in the perfect position to create a culture of quality that gives everyone responsibility for managing their processes, identifying improvement initiatives, and roles are assigned by department heads. The business is small enough that everyone can talk with each other.
The challenges managing quality in smaller organisations is that processes aren’t very established, there are a lot of product/service iterations as the company tries to find its feet, and everything tends to be very new. There may be a lot of manual processing or people investing in lots of different software tools.
The quality manager’s role needs to be focused on understanding what’s working in the business and how this can be repeated to grow. Are you the best at customer service? Are you strongest at utilising new technologies? Quality needs to have data at their fingertips to provide competitive insights.
Before you scale up your department, you may want to ask, “when should I invest in an integrated business management tool?” Investing before you’ve got any processes and procedures to manage makes the maintenance of such a tool an unnecessary overhead. Investing too late means your business will start to become chaotic; employee confusion and frustrations will mount – and you’ll miss risks, opportunities and insights which are key to growing your business.
Medium-sized companieswith 100 to 999 employees
At this growth stage, you should have at least one full time quality manager. Dependent on the context of your organisation – the risks and industry, you may also have people who are solely dedicated to managing documents/processes, audits, health and safety, environment, and/or regulatory affairs. You may decide that training will be owned by human resources or it may sit with quality. You may decide that information security is owned by the technical support or falls under the quality umbrella.
The ‘quality management’ function is centralised. Processes are more standardised, there are established training programs, and there is a fundamental requirement for an integrated business management system where every employee can login and view documents/SOPs, training records, raise risks, issues, manage audit programs, and request change.
Quality managers with fully functioning integrated business management systems spend their time implementing improvement initiatives, understanding customer needs and managing kaizen events – rather than manual processes.
Enterprises
If your revenues are in excess of £500 million, or you’ve got more than 1000+ employees, the structure and scale of your quality team is likely to look very different indeed.
At this stage in the company’s life, you’ll likely develop another layer of management and sub-teams emerge. You will also probably change the structure of your quality management system.
Communication is the greatest challenge for enterprise quality teams. Sharing best practices across multiple sites, managing macro-risks/opportunities, and improving departmental collaboration all put stress on the teams.
At this size, you’ll have executive level quality directors, a team of quality managers, a team of auditors (different for internal and supplier), document controllers, training managers, environmental managers, regulatory affairs specialist, business improvement specialists, process managers, innovation experts, customer success teams – the list goes on!
Enterprise organisations will also need an army of quality engineers to manage the manual processes. Here’s an article on how enterprises BT, Sodexo and Diageo structure their management system: quality.eqms.co.uk/blog/how-multi-site-multi-national-organisations-use-eqms
However, you choose to structure your team, investing in an integrated electronic management system will help drive process efficiencies, help you to scale, and prevent costly mistakes.
Quality World
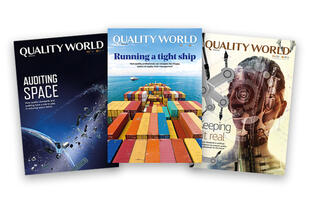
Get the latest news, interviews and features on quality in our industry leading magazine.