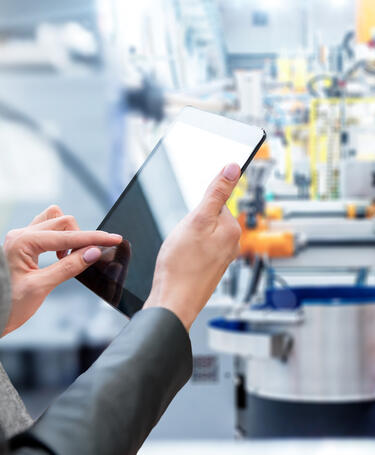
The shared struggle of capturing quality costs
Progress indicator
Robert Oakland, Partner at The Oakland Group, breaks down common challenges and how quality professionals can fuel fact-based decisions.
How can quality professionals foster a culture of data-driven decisions within their organisations?
We’re in an age where we have access to data like never before and quality professionals have an absolutely crucial role in building a culture of fact-based decision making around the data in their businesses. I would say that the key attributes of a quality professional (QP) in this area are to consistently collect the right data and ensure the data quality is good. Once that’s done, the QP then has a role in transforming that data into information and knowledge for the business.
With the right data and the right quality, the QP can turn it into visual information. The QP then needs good governance around that data to make sure that any agreed actions around that data actually happen, that there’s feedback to ensure those actions are delivering the results required and they’re communicating success around those actions, around the improvements made. The QP needs to be restless – never resting, never happy and always looking to raise the performance bar.
What are the most common challenges to capturing the true costs of quality?
The analysis of quality-related costs in any business is an important management tool because it provides the business with a method of assessing the effectiveness of its quality management. It gives you a means of determining the problem areas, opportunities, savings and priorities.
The costs of quality are no different to any other costs in the business. They are like the costs of design, costs of sales, costs of production, or costs of maintenance. They can be budgeted, measured and analysed. A detailed knowledge of these costs is potentially a big driver for improvement.
I believe, and in my experience, opportunities to manage quality costs lie all the way through the value chain.
Many businesses face major challenges and difficulties in capturing these total costs. It’s typical for them to measure aspects of product or service failure, such as warranty claims, inspection, rework and rejects. They tend to be the easier ones you can measure, but it’s much more difficult to measure some of the necessary activities we put in place to prevent quality issues. Many of these quality-related costs don’t sit within the quality department. They sit at various points along the value chain, which means it can be very difficult to identify costs and measure them.
It’s particularly challenging in some sectors such as construction, infrastructure and health care. This is because the value-adding parts of the process are very fragmented, there’s often many parties involved and many of them incur costs. Unless the costs are being recovered by another party it can be difficult and it can be challenging to get people interested in recording costs. People often see these costs as representing low effectiveness of quality management, or people don’t want to talk about it. I’d say the true costs of quality in businesses is much higher than reported in many organisations.
How should quality professionals get buy in from senior leadership?
Getting buy in by using the traditional methods of quantifying costs and driving improvement has been notoriously difficult. It’s often because the root cause of the failure is very complex. It’s difficult to check quality at the end of the product being developed or a service being delivered. It’s also often very hard to prove the benefits. The answer to this lies in data. Data is key, analysis is key.
Quality professionals have an opportunity to lead their organisations and use some of the more advanced, analytical techniques (like machine learning and artificial intelligence). They play a key role in mentoring the business, influencing people and creating that compelling case and encouraging management and others to use a fact-based approach to aid decision making. But it’s important to have softer skills too, to be able coach, talk, convince, influence. A lot of the elements in the CQI Competency Framework.
How would you like to see organisations use machine learning to manage quality costs?
I believe, and in my experience, opportunities to manage quality costs lie all the way through the value chain and you see these opportunities right at the front end from sales and marketing, through to design and engineering, through to production, through to customer and suppliers. I would encourage people to look across their business for common problems and think of how they could be solved with this new lens of data analytics and machine learning.
Think about how effectively you’re deploying resources in a highly variable environment.
For example, it may be that we’ve been struggling for years on low levels of yield on a product within a complex manufacturing process. Can we pull the data we’re collecting on this and pinpoint the hotspots along that process? Or we may have low confidence in the reliability of our products in the field. Can we apply advanced analytics to predict their failure rates and warranty issues?
Another example is billing, which this seems to be a problem for lots of organisations. Let’s say we invoice 20,000 customers, it takes a team of 15 a full month to go through these manually and we receive 10% error rate, so we get very unhappy customers. Could we apply advanced analytics to improve that common and recurring problem?
Think about how effectively you’re deploying resources in a highly variable environment. These are often failure costs, but we may then apply this stuff to prevention and appraisal costs as well to optimise improvement.
Quality World
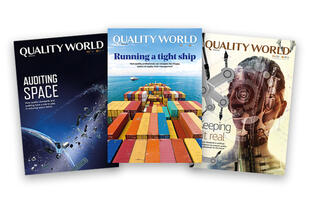
Get the latest news, interviews and features on quality in our industry leading magazine.