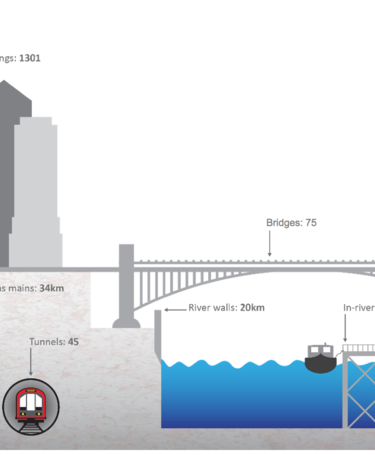
Ensuring quality for the Thames Tideway Tunnel
Progress indicator
In this sponsored feature, Karen Young, head of quality at Tideway, explains how the whole organisation, from managers to clients, is committed to quality and how this affects their most recent project.
1. Can you briefly explain the Tideway project and its importance?
Tideway is delivering the Thames Tideway Tunnel, a 25km ‘super sewer’ that will help tackle sewage overflows into the River Thames. Tideway is aiming to deliver one of Europe’s biggest infrastructure projects in a transformational way – both during construction and in the legacies it leaves behind.
History:
London’s landscape has been shaped by the rivers that flowed through it, connecting to the mouth of the Thames and acting as the city’s natural drainage. The rivers were used to carry waste to the river Thames. The rivers were later paved over and turned into sewers.
By the early 1700s, nearly every home in London had a cesspit beneath it — and the commensurate foul (and often deadly) odours, combined with the Thames’ use as a sewer led to the ‘Great Stink’ in 1858, when the smell was so bad it nearly drove MP’s out of Parliament, and forced Queen Victoria to abandon a pleasure trip on the Thames.
Sir Joseph Bazalgette was commissioned to clean up the river Thames. He designed and constructed interceptor sewers, designed to cut off the combined flow of rainwater and sewage on its way to the Thames and redirected it to East London.
In times of severe storms, the system was designed to overflow through discharge points along the banks of the river, rather than flooding streets and homes. When designed this would have happened once or twice a year. It now happens every week, on average.
Bazalgette had the foresight to design a system that would serve 4 million when the population was 2 million. 158 years on and Bazalgette’s interceptor sewers still form the back bone of the sewerage system today.
London’s population has rapidly increased over and above what Sir Bazalgette had foreseen, now toppling 8 million and as the effects of climate change are no longer imminent but manifesting before our eyes, we have more people, more concrete and more extreme weather. These extreme weather conditions are challenging engineers and scientists alike.
Like many other big drainage infrastructure projects around the world, we are building to last – the tunnel has a life span of 120 years – and to withstand the vagaries of the British weather.
The Thames Tideway Tunnel will start in west London, the main tunnel generally follows the route of the river Thames to Limehouse, where it then continues north-east to Abbey Mills Pumping Station near Stratford. There it will be connected to the Lee Tunnel, which will transfer the sewage to Beckton Sewage Treatment Works.
Built from three main construction drive sites in Fulham, Battersea and Southwark, the Thames Tideway Tunnel is expected to take up to seven years to build, at a cost of £4.2bn (2014 prices). It will require the use of 24 construction sites, 11 of which are located along the river bank.
2. Can you tell us about yourself and your experience of similar projects and quality?
I am currently head of quality at Tideway. My career began as an electrical engineering apprentice at GEC Gas Turbines, moving to Marconi Radar in Leicester, with a period in procurement quality and manufacturing quality engineering, before moving industry and taking up a post as quality manager for a packaging company. There I provided quality assurance and control, for the wet glue and self-adhesive labels production processes for some of the biggest drinks industry companies.
I moved back into engineering and extended my experience in quality management by leading a team of quality engineers, inspectors and test engineers, for the design, build and installation of switch gear, power generation products, process control equipment, traction control and trackside equipment.
I continued with a term in quality management within the rail sector for a sub-contract fabrication company specialising in traction interiors, traction brake frames, lifts and baler systems, before joining a street furniture business. I later returned to the rail sector as quality business partner for Transportation, working on projects such as Crossrail, Victoria Station upgrade, East London Line, and the Stockholm Road Tunnel.
Interfaces with existing infrastructure
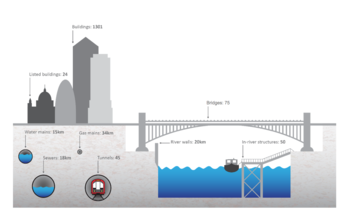
The Thames Tideway Tunnel will be: 25 kilometres long, 7.2 metres diameter, and will be between 30-66 metres deep. It will interface with more than 1300 buildings and 45 tunnels.
3. How is quality structured at Tideway? Can you explain the main challenge facing quality at Tideway.
Tideway (Bazalgette Tunnel Ltd) is the client and employer under NEC, and is a regulated water company. We work as an integrated and collaborative organisation with our contracting organisations (BMB, Flo, CVB & Amey), our programme manager (CH2M), and Thames Water (Tideway Integration Group).
The client quality organisation has set the Quality Policy & Strategy, ensuring that appropriate assurance is in place to ensure the delivery of the Tideway Project in accordance with requirements and obligations, through an audit programme, and performance reviews. We have an integrated management system which is externally certified to ISO 9001. The programme manager ensures the implementation of the strategy through the delivery teams, and monitors the contracting organisations through audits and inspections. The contractors have their own management systems that are also externally certified.
A series of both client led and programme manager led meetings have been established, focusing on quality performance and assurance activity, ensuring that there are clear communication and reporting routes, and that quality risks are identified, mitigated and managed.
The main challenges are raising the profile of quality within construction, and getting the industry to recognise the importance of quality. Improving quality competences and understanding at all levels, with the right behaviours and governance, is equally challenging.
4. What benefits or solutions are you trying to achieve through quality?
Construction is a long way behind manufacturing when it comes to recognising the importance of getting things right first time, and of using Lean and Six Sigma tools and techniques to help us work smarter, better and safer. We want to lead the way in the construction industry, improving productivity by promoting lean thinking and continuous improvement and by working collaboratively with our main works contractors and supply chain
5. What tools are you using to deliver improvement?
Tideway is looking to introduce a continuous improvement programme across the whole organisation.
We are encouraging the open identification of issues and opportunities that can be investigated, solved and shared as best practice, by using a variety of ‘quality tools’ with ongoing training, coaching and support.
Continuous improvement will form part of the agenda in meetings and quality forums, and we are aiming to ensure that lessons learnt will be carried out effectively and efficiently with knowledge sharing.
6. How do you engage staff in quality across the business?
Quality is not seen as being a sexy or exciting subject, so raising the profile and engaging people in its importance is quite difficult. We are trying to use a number of different approaches, including:
- The engagement of people in the continuous improvement activity.
- The communication and promotion of the intranet based management system, which has recently been enhanced and improved.
- Planning regular communications in relation to quality related topics.
- Trying to bring a bit of fun into understanding what quality is all about. For instance, for last year’s World Quality Day, we had a paper plane making competition, quality related word searches, and crossword puzzles.
7. What are your views on emerging talent in quality in your business and the wider industry? How are you supporting the next generation in quality?
One of Tideway’s legacy commitments is ‘to inspire and up-skill a new generation.’ To be able to improve quality in the construction industry, we need to improve learning, and competency in all areas of quality. So, I am keen to promote quality apprenticeships and/or increase training and awareness of quality tools and techniques within other apprenticeship schemes.
Quality World
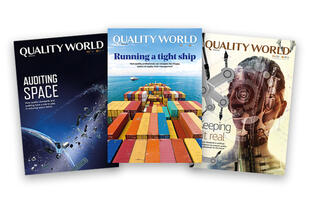
Get the latest news, interviews and features on quality in our industry leading magazine.
Partner with us for the next event
If you are interested in sponsoring our next event, please contact our Event Manager Katie Steingold