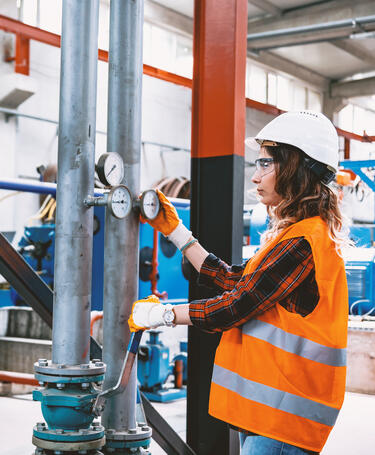
Dealing with incorrect information

In our latest dilemma, find out what to do when a company appears to have supplied duplicate testing images in order to meet the delivery requirement.
Dilemma
A customer quality engineer is conducting a release inspection at a manufacturer of high-pressure ball valves. The valves are for a pipeline project in northern Alaska.
The contract requires full radiographic non-destructive testing of the welds for the flange ends of four valves. The engineer asks to view the radiographic plates of the welds, which show that no significant weld defects are present. However, he notices that four of the plates contain several small white pinpoints in identical places outside the weld areas.
He asks the production manager about this and is told that these marks were likely to have come from the radiographic film and can be disregarded. When asked why the marks appear in identical places, the manager replied that the film negatives probably came from the same batch.
The engineer has previously encountered similar marks on radiographic plates, but never in identical places. He suspects that these plates could be four images of the same weld. He is aware that his company requires the valves to be shipped to Alaska the next day.
What should he do?
Response
First there needs to be a meeting with the quality lead, the internal staff member or sub-contractor qualified to perform the non-destructive testing (NDT level III), and the radiographer. They need to discuss the customer’s concerns and agree on the investigative action. Ask for the documentation from the film package, perform a full review of the package and make sure the operator followed the correct procedure and performed the radiography in accordance with the stated technique instruction sheet. Ask to see the level II radiography qualifications to verify that the level II radiographer’s approvals are correct for the type of material and product forms.
The production manager stated they were film marks, so based on this, customer quality engineer should check the batch of films being used. He should make sure they are being stored as per the manufacturer’s recommendations, verify the expiry date and see that the checks of the film processor have been completed and documented.
If all the above checks are satisfactory, then he should make a visual inspection and/or penetrant inspection of the valves to check if the indications on the film show up on the welds. If there is an indication after the additional tests, he should ask for the radiography to be performed again with a new batch of films in the presence of the production manager and NDT level III. If there are no indications visible after the additional tests, then they should produce a corrective action report, detailing the description of the problem, disposition and close out. After this, all parties should agree to ship the valves.
If the indications are still visible during the review of the new radiographs, then the valves should be rejected and not shipped, and nonconformances issued.
It should be stated that for the next order, the client’s inspector should be given the inspection and test plan, so that he/she can add any additional hold points. He/she should also ask to be notified in a timely manner in order to attend and witness the activities deemed necessary.
With thanks to Ian Dunlop BSc, CQP FCQI, for providing the scenario, and John Randles, PCQI, Supervisor Code Services, for providing the response.
If you have a dilemma you think we should include in our new Auditor Dilemmas series, please email [email protected]