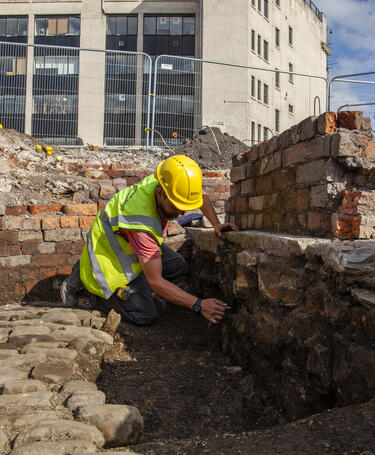
Digging deep towards integration: Wessex Archaeology
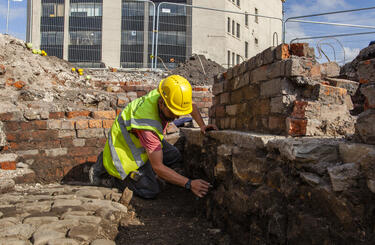
An archaeological services company has encouraged employees to volunteer as auditors as part of the journey to implement ISO 45001 and integrate it with an existing quality management system. We spoke to Wessex Archaeology’s Quality Director, Linda Coleman PCQI, and some of her colleagues, to find out more.
Professional archaeological and heritage advice services company Wessex Archaeology (WA) achieved the ISO 9001 quality management standard in 2015.
By early 2020, however, its Quality Director, Linda Coleman PCQI, had identified that its occupational health system (OHS) was in need of a refresh. So she started the company on the journey to achieve 1SO 45001 occupational health and safety certification.
Coleman was also keen that WA, with offices across the UK, should link the ISO 45001 standard with its existing quality management system (QMS). According to Coleman, the journey towards integration has so far highlighted three key challenges and solutions.
Challenge 1: performance evaluation
In a constantly evolving business sector, maintaining sufficient resources to keep a management system effective is often a challenge, explains Coleman. “You need people who can really engage with the continuous improvement approach.
“We began our journey towards integration in early 2020, by inviting expressions of interest from our staff to become auditors for integrated management systems (IMS), covering ISO 9001:2015, ISO 45001:2018 and ISO 14001:2015. Eight employees were chosen from 20 applicants to join our HR director and me at the training.”
Linking existing systems to ISO standards is complex.
First, these staff members were required to have a good understanding of one of the standards – and ISO 9001 was the obvious choice. “I spent two days running through all the standard’s clauses and the WA QMS so they were prepared,” says Coleman. “It was a significant investment for the company to bring staff together from across our regional offices and teams for two days’ informal training. This was followed, a few weeks later, by the BSI Training Academy Course.”
Challenge 2: support
WA’s OHS specialist, Ian Smart, was new to the business, having joined in April 2020, just after the first coronavirus lockdown began. He arrived with 20 years’ experience as a safety professional, mostly with the UK Health and Safety Executive, but he had never implemented ISO 45001. According to Coleman, it was important to support Smart, and allow him time to read and explore the standard, as well as WA’s existing OHS.
Smart agrees: “You first have to understand the way your organisation works – ‘the context’, as Clause four of ISO 45001 clearly puts it. Otherwise, in seeking to comply with ISO 45001, you may evolve the OHS in a way that is less effective.
“While this was undoubtedly more challenging because of the demands of the Covid-19 situation, I was greatly helped by the WA QMS that was already in place, and the support that Linda could supply through her experience of implementing and running that system.”
Training was also important, and Smart took the ISO 45001 auditor course once he had familiarised himself with the standard. “The course was really useful. Going over the detail of the standard reinforced what I had read myself and what I had been discussing with Linda.”
The OHS team at WA is managed by HR Director Angela Batt. Her experience of IMS audit training gave her the insights needed to help lead and support the team on their certification journey.
“Linking existing systems to ISO standards is complex,” says Batt. “We needed to understand the requirements and then identify how we, as a business, align with each clause, and the evidence we have to support it. It’s about translating the clauses into a language you and the business are more familiar with. This is where the general guidance documents that support the standards are really useful.”
Challenge 3: improving the effectiveness of the management systems
Coleman points out that a mature management system is not always as effective as might be hoped: “Yes, it may work, but how do you review and refresh it when, like me, you’ve been living and breathing it for six years?”
Her solution was to get a fresh pair of eyes on the case – an additional person focused on the QMS, but also looking at where the synergies with the occupational health and safety management systems (OHSMS) lay.
This person was Quality Specialist Sandy Taft, who started with WA in August 2021 – and she was rather daunted at first. “The biggest challenge I faced coming into my new role at Wessex was that our QMS was much larger than anything I had worked with previously,” she says. “The first time I looked at the QMS documents, I felt a little overwhelmed. My first tip for anyone in a similar situation is not to put too much pressure on yourself. Take things day by day and remember to ask questions.”
Taft spent several weeks stripping down and analysing the systems to understand how they fitted into the business, its processes, the services WA provides, and the requirements of the standards. “By taking this approach, I could map out similarities between the systems, highlighting where integration would be possible. My second tip for anyone looking to integrate their systems would be to remember that, although the requirements may be the same or similar, what works for one system does not always work for the other system.”
Coleman sums up: “With these measures in place, great teamwork and good support from our senior management, we are well placed for our Stage 1 ISO 45001 audit in January 2022.
“We will have both systems integrated by the end of March 2022 and have already started looking at implementing the ISO 14001 environmental management standard. We’re learning a lot as we go along and our aim, of course, is to continually improve.”
Learn more about ISO 45001.