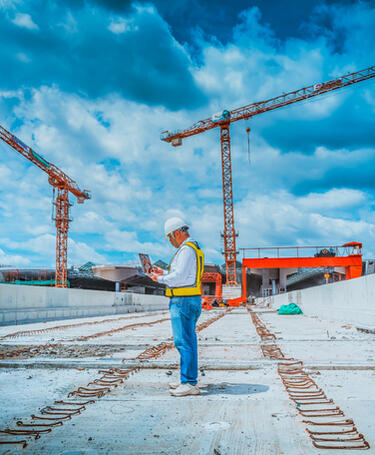
Implementing a quality control management system
Progress indicator
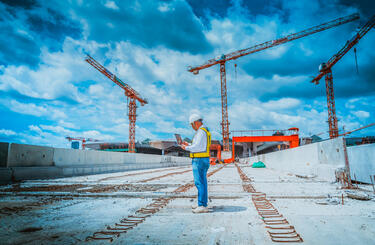
Dalvinder Singh, Quality Coordinator at NG Bailey, explores the pros and cons of adopting a quality management system to ensure a right first time approach on projects in the construction sector
Implementing a quality control management system (QCMS) within NG Bailey has been an ongoing process and one that I have been involved in since joining the business and the industry three years ago. At NG Bailey, we are enhancing our system and bringing it online to meet the demands of the business and make the process slicker for our people and for a wide range of processes, such as drawing development and control, quality inspection management, daily diaries and bracketry design.
Issues resulting from poor quality can be extremely costly. Research from the Get it Right Initiative has indicated that avoidable errors are costing the construction industry around £20bn per year.
Unlike a car manufacturer, where the same product is assembled more than once under controlled conditions, every project in the construction sector is completely different and this makes managing quality more challenging.
Recent high-profile failures across the UK, such as the Grenfell Tower fire, have led to quality being high on the agenda for all companies across the industry. An independent review of the building regulations and fire safety, The Hackett Report, has highlighted the need for a new framework designed to create a more simple and effective mechanism for driving building safety.
My background in the automotive sector has allowed me to compare both industries and I believe that construction in the UK is experiencing a decline in quality due to the following factors:
- Disadvantages of subcontracting
- Pros and cons of varying procurement methods
- The increasing complexity of buildings and their engineering systems
- An engineering skills shortage and lack of good quality training for apprentices
- The increasing use of modular engineering systems which can be installed by unskilled operatives.
In order to address these issues within NG Bailey, we have developed a series of tools and processes to simplify and standardise our approach to quality control across the business.
Central to this project was the introduction of a digital platform to carry out visual quality checks and inspections while on site. Working closely with the developer SnagR, we created a visual inspection-led approach that enables us to gather useful analytics and performance data across a wide range of projects. We act on this data to implement an ongoing programme of lessons learned and continuing professional development initiatives.
This approach to managing quality is a fundamental change in the industry as well as within NG Bailey, and there are pros and cons…
Pros of the QCMS include:
- A systematic and auditable way to keep and store data
- Easy mechanism to prove competence
- Reduce time filling out forms
- Everything is accessible and stored on a virtual network
- User-friendly software for visual inspections and capturing issues
- Full accountability and traceability of all visual inspections and issues
- Able to standardise all projects.
- Compare and contrast analytics/KPIs
Cons of the current QCMS include:
- Fear of change from colleagues
- Lack of awareness among colleagues
- Lack of training for employees.
Through my experience of implementing the QCMS, I’ve learned that change can be a challenge in the construction industry. Some people are hesitant to move to digital systems, which is often due to a lack of upfront engagement or understanding.
At NG Bailey we acknowledge these issues and are actively working to continuously improve. This is done through delivering regular training sessions where internal and external stakeholders are educated on our approach to quality management. To date, I have delivered over 150 training sessions to more than 1,000 colleagues and supply chain partners.
Quality can be seen as a job for the quality team rather than for everyone onsite. However, successful quality management comes from a culture where everybody takes responsibility throughout the project.
What do we want to achieve?
Focusing on quality management during the preconstruction stage can help to engage all of the stakeholders involved in a project, procure the right materials from a preferred supply chain and ensure everyone involved is suitably qualified and experienced.
We aim to complete our projects to budget within the timeframe allocated and to the highest quality standards, while still making a profit. Having a right first time approach may cost more upfront, but the benefits in the long-run far outweigh the monetary cost of adopting this approach.
Managing and implementing a QCMS within the construction industry, and specifically here at NG Bailey, is essential for business continuity and we see that getting things right first time is a vital step in achieving our goals. Since tragedies such as the Grenfell Tower fire, this approach to managing quality has only intensified.
Implementing a successful QCMS requires a monetary investment and time, you also need to win the hearts and minds of your colleagues, and a supply chain that works for you. Changing that behaviour and attitude has been and will continue to be a difficult process, but with good training, workshops and a consistent message, it is achievable as we have shown at NG Bailey.
Quality World
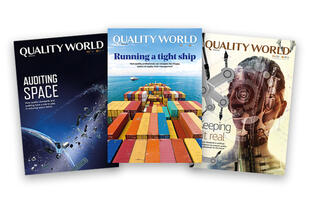
Get the latest news, interviews and features on quality in our industry leading magazine.