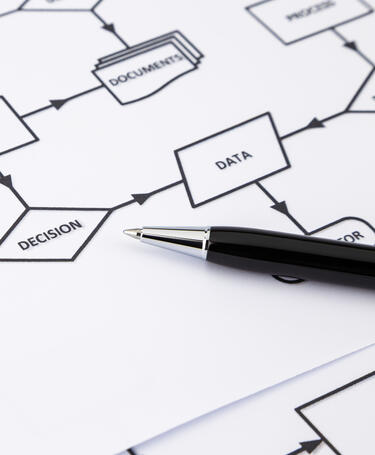
Integrating FMEA into process development
Progress indicator
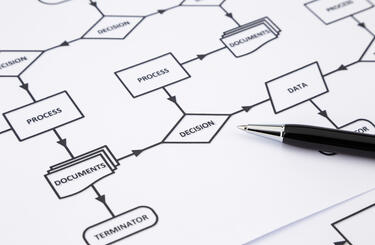
Find out what happened when Benetel integrated FMEA into their process development for ISO 9001:2015.
Benetel is a telecoms infrastructure provider, delivering custom and off the shelf solutions to the market. Benetel is specifically focused on Public Safety, Private LTE and Disaggregated RAN.
Infrastructure development and design processes include mechanical, hardware, RF and thermal design, verification and validation, software development and manufacturing. The organisation is ISO 9001:2015 certified and had recently identified opportunities to strengthen risk management at the process level.
The company leveraged its use of Lean Six Sigma to develop VIPIR, a methodology that is now used when developing all Benetel processes. VIPIR is an acronym for Visual Identification of Processes Integrating Risk Management.
Robust processes are important to us, as we need to minimise the opportunity for error in our design and validation processes
The approach is simple – before documenting a process, Failure Modes Effect Analysis (FMEA) is conducted. FMEA helps capture potential failure modes and risks at each step of the process.
The second step used by Benetel is the creation of process flow charts using process mapping.
Process owners and their teams, with assistance from quality assurance, then analyse the process flow chart and integrate risk mitigation for each of the identified failure modes and risks.
“Robust processes are important to us, as we need to minimise the opportunity for error in our design and validation processes. That is why VIPIR has become a key tool in process development. VIPIR has helps us identify new process steps, and in some cases, new sub processes to mitigate risk,” says Susanne Carpenter, CQP MCQI, Quality Manager at Benetel.
Taking the company’s non-conforming outputs process as an example, FMEA quickly established a link between the management of suppliers and supplier corrective action and control of non-conforming materials. FMEA also identified the link between non-conforming materials and the inability to supply prototypes to customers, leading to customer dissatisfaction.
Communication of material shortages to the senior management team and the identification of at-risk deliveries was identified as a critical risk. Other risks identified included use of non-conforming components and subassemblies in customer product.
Integrating the process FMEA risk mitigation into the non-conforming outputs process has changed its content. Benetel identified the need to add a sub process for supplier corrective action to eliminate supplier-based non-conformances. The process highlights the work of the Material Review Board and added additional controls in this area.
A new sub-process was added – stop ship alerts – that communicate customer deliveries that are at risk due to material supply issues. An alert is sent to the senior management team, operations and the relevant engineers to advise them of an issue, the product affected and the likely consequence for the customer.
The positive impact of VIPIR has encouraged Benetel to integrate further Lean 6 Sigma methodologies, including DMAIC and 8 step problem solving. Adrian O’Connor, CEO of Benetel says “Innovative use of Lean 6 Sigma tools is driving us to not only meet but exceed our customers expectations.”
Quality World
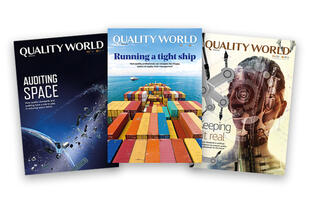
Get the latest news, interviews and features on quality in our industry leading magazine.