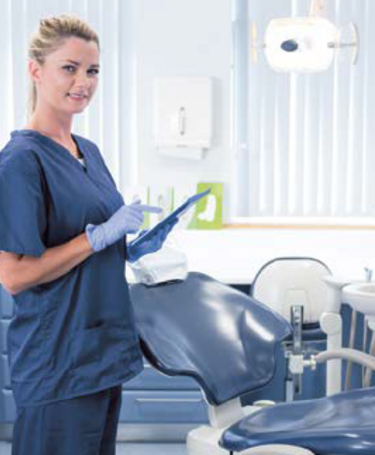
Integrating quality in the design of dental tools
Progress indicator
Manufacturer Dentsply Sirona shares the stages involved in the design of their dental equipment products.
In the dental industry, the quality function plays a critical role in safeguarding the health of patients. Well-known dental device manufacturers integrate quality tools in the development and production of medical equipment.
Dentsply Sirona is one such company. The global manufacturer develops, manufactures and markets dental and oral health products. With 15,000 employees, Dentsply Sirona operates in more than 40 countries and has a market presence in more than 120 countries. The company spends more than $125m (£90m) annually towards dentistry research, and has a research and development platform that includes more than 600 scientists and engineers.
Hannah Seevaratnam, Director of Quality Systems, Quality & Regulatory at Dentsply, said that product development and production involves a company-wide quality system software, a standard design control process, root cause and risk management methods, and robust quality policies and procedures.
Medical devices standard ISO 13485 underpins the design and development controls at Dentsply Sirona’s facilities.
“Dentsyply Sirona’s applicable locations are certified to ISO 13485 which is the internationally recognized standard that governs design and manufacturing of medical devices; and as such, is the basis of the Dentsply Sirona’s quality management system,” said Seevaratnam.
Controls in design and process
Dental professionals act as key opinion leaders during the design of a new product, Seevaratnam said.
“Design has a power of persuasion that plays out on many different levels of perception. We take advantage of this potential for the items,” said Thomas Nack, Head of the Design and Development of Dentsply Sirona treatment centres at the Bensheim, Germany site. The products are designed based on the needs of clients and their teams.
“Every product model has its own requirements coming from the dentist and assistant elements, in order to realise different comfort requirements in the treatment room.”
Symbols play a critical role in the control system, which can sometimes be a longer development process. A team of experts are consulted to find an intuitive symbol that reflects a corresponding function at first glance. The team’s objective is to maintain a level of continuity in the controls while allowing for the smooth integration of new technical elements.
“There are an awful lot of dependencies to observe that we always have to coordinate from both development and design perspectives,” adds Nack.
He explains that the idea for a new product comes from the functional and aesthetic needs of the customer and the market. The team conducts investigations and considers the existing technical innovations and market requirements. Upon receiving relevant product requirements and functional specifications, the team then researches the current trends and design developments in the dental sector.
“The product managers have significant influence on the functional and aesthetic design,” said Nack. “Designers and hardware and software developers design the individual components and parts right down to the smallest details. The electrical engineers ensure that the electronics can be accommodated in the housing units. The technologists check whether suppliers can manufacture certain projects and parts.”
Products are then tested at various intervals to business and regulatory requirements before they are released, said Seevaratnam. “The processes are routinely audited for compliance.”
For example, the design of the dental chair considers the dentist, the dental assistant and the water unit.
“Experts who are specialists in their fields come together from their areas,” said Nack. “Fitters check whether and how the device can be assembled. Then, our colleagues from the After Sales division ensure that the centers and devices can then later on be serviced.”
Options for packaging and storage also play a role in the development of a new product.
“Material and design are mutually dependent on each other and hence we are continually developing the use of new materials,” said Nack.
At the company’s research division, the teams are engaged in more than 50 clinical studies at any point in time. The teams test innovations to determine if they are safe and effective.
Quality World
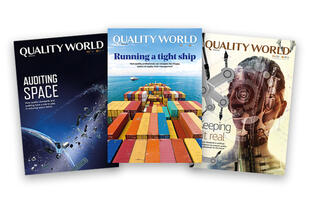
Get the latest news, interviews and features on quality in our industry leading magazine.