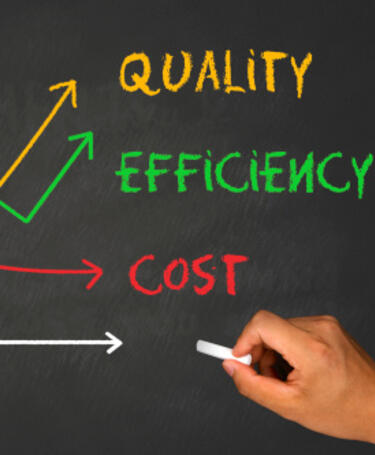
ISO 9001:2015 and calculating the cost of quality
Progress indicator
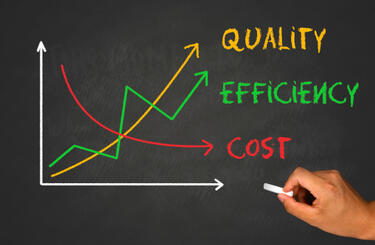
Bob Hughes introduces the tools and principles to effectively report quality costs.
In the quest for quality excellence, there is a significant need for companies to have a greater awareness of the cost of quality.
As a quality management consultancy (Temple Quality Management Systems), we have observed that very few organisations make any reference to the cost of quality in their management review.
Risks associated with quality costs can slip under the radar but identifying these risks is fundamental for organisations when implementing continuous improvement processes.
For example, identifying the risks can benefit companies when they undertake a thorough plan, do, check, act (PDCA) improvement strategy.
At this time of year in particular, it’s ideal for companies to establish new organisational objectives and targets.
Reducing cost through using a process approach will allow organisations to determine whether they are adding costs or value.
At this time of year in particular, it’s ideal for companies to establish new organisational objectives and targets.
Risk-based thinking, PDCA and the process approach form an integral part of ISO 9001:2015. The benefit of using these methods includes the better use of resources and increased accountability.
In accordance with the standard, quality professionals should consider if they have a designated person to take overall responsibility for coordinating and reporting quality costs.
When it comes to introducing products, how effective are quality professionals at planning the full lifecycle? This should include effective up-front planning, management of waste, creation of process documentation and the correct frequency of relevant inspections.
Companies should also ask themselves if they have knowledge of compliance costs, including the cost of relevant specifications.
Quality costs are usually big but there are many models available that can be used effectively to measure the actual cost.
Identifying and collecting quality cost data can be difficult but quality professionals need to rise to the challenge. Identifying prevention, appraisal, failure, and internal failure costs can help when producing the data.
Prevention quality costs include staff training and market surveys. Appraisal costs can be anything from incoming goods inspection to proofreading. Internal failure costs can include the cost of scrapped material and rework and repair costs. Examples of external failure costs can include product recalls, customer complaint handling and loss of reputation.
We recently identified a cost reduction of £7,000 a year at one company. We realised the over-complication of calibration, with no evidence-based thinking, had become the norm.
We also noted at another manufacturing company that the customer-specific requirements were not always effectively determined. For example, no boundary samples had been agreed or signed off and in some cases, the visual appearance of the items was not clear.
Quality costs are usually big but there are many models available that can be used effectively to measure the actual cost.
It is important to ensure you have an accurate representation of costs so that management can use the information to develop accurate action plans and implement improvements crucial to the company’s success.
Bob Hughes, CQP FCQI, managing director at Temple Quality Management Systems