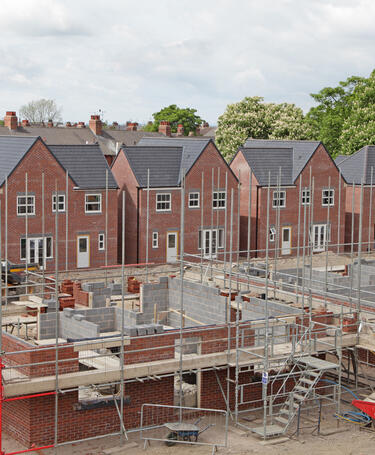
The UK’s New Homes Quality Board ‘Code of Practice’: a closer look
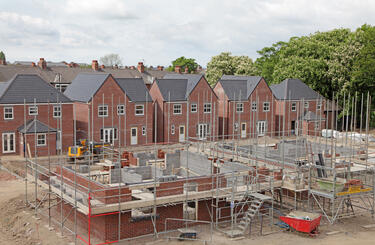
The recently launched New Homes Quality Board, and the soon-to-be launched ombudsman, are a response to recommendations made in a 2016 report titled ‘More homes fewer complaints’. Upon closer inspection, however, the Code of Practice raises some concerns.
The All Party Parliamentary Group for Excellence in the Built Environment’s report ‘More homes fewer complaints’, published in 2016, is a report from the Commission of Inquiry into the quality and workmanship of new housing in England.
With the New Homes Quality Board established, and the ombudsman launching soon, the new arrangements aim to “plug the gaps in existing protections and aim to deliver consistently high-quality homes and considerably stronger consumer protections”.
The whole system is based on a Code of Practice based on 10 principles, and four sections covering:
- selling a new home
- legal documents, information, inspection and completion
- aftersales, complaints management and the ombudsman
- solvency, legal and jurisdiction.
At first glance, this code may seem adequate – we see similar codes in sectors such as automotive sales focussed on eradicating bad actors. However, dig a little deeper and some contentious requirements can be found.
In most other business-to-consumer (B2C) sectors, it would be deemed as unacceptable to delegate quality control to the consumer, or to require a reminder that the producer should carry out some quality control itself. However, the requirements suggest just that:
“The developer must provide for an opportunity for the customer to appoint an accredited professional to carry out a pre-completion inspection check.”
“At the point of completion the developer must have carried out their final quality assurance inspection of the New Home and provide a customer with a schedule of any incomplete works or defective items, and a statement of timescales for completing / remedying such items...”
This code implies an acceptance that some house builders operate without any form of quality assurance, and they and their customers will have to rely on final inspection and inevitable rectification. This does not happen in the automotive or mobile phone industry, perhaps partly because demand-and-supply is balanced in favour of the consumer and companies have to compete on quality.
Of course, some may say that building houses is not like manufacturing. I would argue that building a house is a repeatable and improvable process, much like manufacturing. The rest of the construction industry is enthusiastically embracing quality management. For example, the UK Get It Right Initiative (GIRI) has recognised that getting it right is key and can be developed with the right leadership, training, culture and management system. They have even worked out that getting it right first time not only satisfies customers, but also improves safety and saves companies money.
A quick read of some house builders’ annual reports indicates that there may be some quality-washing going on, with fine words about ‘right-first-time' and ‘creating value for customers’. Alternatively, they may indeed be on a quality improvement journey. One measure may be when we can remove all the questionable inspection details from the code of practice.
Find out how using ISO 9001:2015 can raise quality in Myanmar’s construction sector.