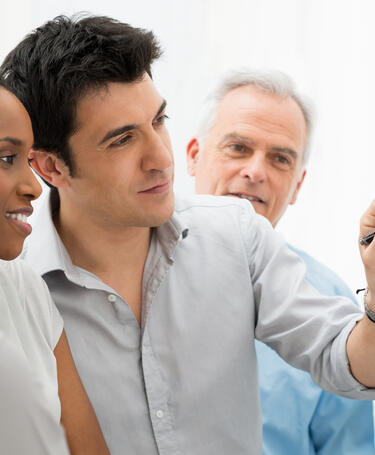
The origins of Lean Six Sigma
Progress indicator
This sponsored feature from Catalyst Consulting Ltd explores the history and techniques of applying a continuous improvement framework. This is an edited extract from Lean Six Sigma for Leaders by Martin Brenig-Jones and Jo Dowdall of Catalyst Consulting
Over the last few years, Lean Six Sigma has come to mean a number of things, but in reality most organisations use it as a tried and tested approach to implement continuous improvement.
At Catalyst, we use the name to encompass a wide range of methods, tools and techniques that have their origins in different histories and backgrounds. This range is developing and changing over time as more and more organisations build ever increasing experiences of using the approach in very different organisations.
The latest most successful implementations of Lean Six Sigma bring together thinking, principles, approaches, tools and techniques from:
- Lean Thinking
- Six Sigma
- Change Management
- Agile
- Digital Transformation.
Lean Thinking
If you’d like a serious grounding in Lean and Six Sigma then pick up a copy of Lean Six Sigma for Dummies. When we wrote that book we wanted to ‘demystify’ the approach and make it accessible to everyone. We are going to paraphrase some of the basics here with the emphasis on the leadership aspects behind the approach.
When people talk about the roots of Lean Thinking, the word ‘Toyota’ is often quoted. Toyota calls their system the ‘Toyota Production System’ (TPS). The concept of the word ‘Lean’ goes back to 1987, when John Krafcik who is now the CEO of Waymo (including the Google driverless car project) worked as a researcher in his earlier career at MIT. He was looking for a label for the TPS phenomenon that described what the system did. On a whiteboard, he wrote the performance attributes of the Toyota system compared with traditional mass production. Those attributes were:
- Needed less human effort to design products and services
- Required less investment for a given amount of production capacity
- Created products with fewer delivered defects
- Used fewer suppliers
- Went from concept to launch, order to delivery and problem to repair in less time and with less human effort
- Needed less inventory at every process step
- Caused fewer employee injuries.
Krafcik concluded: The system needs less of everything to create a given amount of value, so let’s call it Lean.
The Lean Thinking world grew rapidly with a focus on reducing non-value adding activities or waste. The Japanese word for this kind of waste is Muda.
But to sustain success, organisations need a lot more than knowledge about the tools and techniques. It all boils down to leadership. After all, Lean Thinking would not have taken root in Toyota if it didn’t have strong leadership commitment to create the environment needed to embed the principles and thinking into the organisation as a system.
As Toyota chairperson Fujio Cho said: “The key to the Toyota way is not any of the individual elements but all the elements together as a system. It must be practised every day in a very consistent manner — not in spurts. We place the highest value on taking action and implementation. By improvement based on action, one can rise to the higher level of practice and knowledge.”
As we said in Lean Six Sigma for Dummies, the system focuses on training to develop ordinary people and teams that follow the company’s philosophy to gain exceptional results. Consider the following:
- Toyota creates a strong and stable culture wherein values and beliefs are widely shared and lived out over many years.
- Toyota works constantly to reinforce that culture.
- Toyota involves cross-functional teams to solve problems.
- Toyota keeps teaching individuals how to work together.
Being Lean means involving people in the process, equipping them to be able, and feel able, to challenge and improve their processes and the way they work. Never waste the creative potential of people!
All of the above has implications for Leadership. It won’t just happen without commitment and ‘commitment’ alone isn’t enough either — you will need to stir it into action.
There is a lot more to Lean Thinking but these five principles underpin the approach:
- Understand the customer and their perception of value.
- Identify and understand the value stream for each process and the waste within it.
- Enable the value to flow.
- Let the customer pull the value through the processes, according to their needs.
- Continuously pursue perfection (continuous improvement — or Kaizen in Japanese).
Behind Six Sigma
Lean has its origins in Japan, while Six Sigma has its roots in the US from the 1980s (when we can trace the origins to Motorola). Then CEO Bob Galvin was struggling to compete with foreign manufacturers and Motorola set a goal of tenfold improvement in five years, with a plan focused on global competitiveness, participative management, quality improvement and training. Quality engineer Bill Smith coined the name of the improvement measurements: Six Sigma. All Motorola employees underwent training, and Six Sigma became the standard for all Motorola business processes.
The word soon spread around major American businesses including Allied Signal. In the ’90s, the concept reached Jack Welch, the dynamic CEO of General Electric (GE). Welch was initially sceptical as he viewed Six Sigma as a ‘quality’ programme, but he agreed to pilot test the approach insisting that all Six Sigma projects should have a clear measure of success. The expression Return On Six Sigma or ROSS was born. Within a few months it was clear that Six Sigma projects could return attractive financial benefits and Welch dictated the use of Six Sigma across the entire group of GE businesses.
Once again, it was strong leadership (Welch was known in GE as ‘Neutron Jack’), albeit a very different style of leadership compared with Toyota, that drove the successful implementation of Six Sigma. Through GE’s experience, the world learned that Six Sigma was far from ‘just a quality programme’ and that the approach was proven to work in all kinds of businesses not ‘just manufacturing’.
When Jack Welch introduced Six Sigma, he said: “We are going to shift the paradigm from fixing products to fixing and developing processes, so they produce nothing but perfection or close to it.”
The recognition that it is the ‘process’ that needs to be changed is central to both Lean and Six Sigma. Six Sigma enhances the Lean approach considerably. For example, Six Sigma has strong roots with measurement and data analysis. It extends a great Lean toolkit by bringing a range of additional tools focused on how to measure, how much to measure and statistical tools, many of which are relevant for everyone in business or leadership roles.
Six Sigma also brings a powerful problem-solving method that can easily be integrated with Lean tools. This method has now become the standard problem-solving approach for many organisations and has stood the test of time and application in different sectors. The original thinkers in Motorola who devised the Six Sigma method must be astonished at how this approach has spread throughout the world and is still growing in popularity more than 30 years since it was first conceived.
I have occasionally heard leaders say “we are not ready for Six Sigma” and this is almost always down to confusion about the name ‘Six’ Sigma.
When the statisticians in Motorola influenced the creation of the name ‘Six Sigma’ they had the right intentions. They wanted to set an aspirational goal for everyone — produce a very high level of quality. However, to understand exactly what they meant by Six Sigma requires a rather complicated, mathematical explanation that is likely to turn off many leaders before they reach a real understanding. To be honest it isn’t technically that relevant to a lot of applications of continuous improvement, which can benefit from the principles behind Six Sigma and the tools underpinning it. The name stuck though and has entered the business vocabulary whether we like it or not.
While we agree that the name ‘Six Sigma’ can be an issue, don’t get too worried about it. Some of our clients feel strongly enough to use a different ‘brand’ instead of Lean Six Sigma. Here is a selection of the names we have seen over the years:
- Operational Excellence
- Business Excellence
- Think Process
- Continuous Improvement
- Continuous Innovation
- Relentless Simplification.
We’ve also seen ‘coded’ expressions that mean something specific for a particular organisation — like ‘e3’.
In all these cases, when you look ‘under the bonnet’ you will find the same approaches, principles and tools that come from the latest Lean Six Sigma stable. Make it work for you, adapt it for your organisation, make it fit so that people feel curious and want to join in.
Lean Six Sigma principles
In summary, Lean Six Sigma is based on a set of principles which are drawn from the worlds of Lean and Six Sigma as mentioned above:
- Focus on the customer.
- Identify and understand how the work gets done.
- Manage, improve and smooth the process flow.
- Remove non-value-added steps and waste.
- Manage by fact and reduce variation.
- Involve and equip people in the process.
- Undertake improvement activity in a systematic way.
Wiley Business Books commissioned Lean Six Sigma for Leaders and will publish the book in April 2018.
Learn it
Martin Brenig-Jones runs a regular free one hour webinar on Lean Six Sigma.
To sign up or to find more information, visit https://lean-six-sigma.training/lean-six-sigma
or contact Catalyst at catalystconsulting.co.uk
Quality World
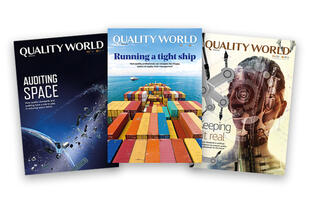
Get the latest news, interviews and features on quality in our industry leading magazine.
CQI International Quality Awards
Six awards, recognising quality professionals who contribute most to their organisations.