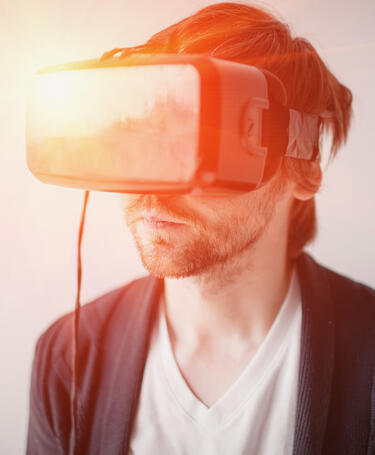
Breaking the rules of reality
Progress indicator
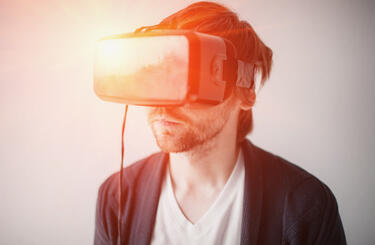
It's been heralded as the future of product creation and it's even creeping into our everyday lives. William Lord at Rolls-Royce Nuclear speaks with the CQI about how virtual reality is revolutionising manufacturing.
Virtual reality (VR) is fact becoming the biggest digital trend for 2016, and this futuristic technology is weaving its way through imaginations across the globe. From Google’s virtual school field trips, where students embark on an immersive journey to Machu Picchu, to virtual American football practice in the NFL, every industry is cashing in on the craze.
The implications of VR for manufacturing are huge, but so far most businesses are failing to maximise its potential.
The benefits seem infinite and the technology means companies can test designs and scenarios so products can be experienced before they have been produced.
One organisation harnessing this innovation is Rolls-Royce.
In a soundproof room at the heart of its nuclear facility in Derby, operations, manufacturing and quality professionals can don a pair of sleek black goggles and find themselves transported to the manufacturing floor.
They can enlarge a single cog in a complex machine or look through walls to find inefficiencies, while teaming up with the design function to create solutions to problems instantaneously.
Let’s not forget all this can be done from the comfort of an office, before the product or the factory has even been created, making this the cutting edge of manufacturing technology and essential for achieving right first time.
A virtual revolution
Rolls-Royce began its virtual reality journey in 2014 and the technology has revolutionised the way the company operates.
Its nuclear business is using the system, designed by virtual reality experts Vertalis, to improve its use of lean principles.
Reducing bottlenecks on the factory floor and solving the challenges of facility creation and product movement, as well as product realisation.
The company was the first in the UK to invest in the 4K projector system, which is capable of a higher resolution and brighter image, and in little more than a year the organisation has made a mammoth cost of quality saving of £1.8m, proving the investment was worth its salt.
“Now we can look at products and understand how we can transport them through the factory, how we should handle the product and what storage we can use,” reveals William Lord, CQP MCQI, pre-production delivery manager at Rolls-Royce.
“We can then look at the processes to find out if we need additional equipment.”
Lord has been involved in virtual reality at Rolls-Royce from the start and now he runs the VR facility, managing 30 personnel across three teams which work across the different business functions, while making sure the technology is continuously improving business practices at the nuclear powerhouse.
“When I look back to the foundation of my career at Toyota, we were really into lean methods but everything was done on paper and cardboard cut-outs,” he says.
“The methodology was really good but virtual reality gives you another dimension. It allows you to visualise and get a real sense of the product or service. You can have a scale of 1:1 so you can manipulate different environments.
“We’re using the tools and techniques of the quality portfolio to create a structure around how to use the technology, including policies, procedures and a method for our reviews,” says Lord.
The power wall
Today up to 20 people can meet in the virtual reality suite – meaning different employees from across the business can slip on the goggles and be transported into a simulated world.
The virtual reality screen, named the ‘power wall’ takes up an entire side of the studio, ensuring anyone can benefit from the full effect of the technology and give their feedback on the product or process they are viewing.
Everyone from apprentices to senior management uses the headset, meaning each member of staff can get to grips with quality on the factory floor.
Now, the barriers between teams are disappearing and Lord notes the technology has helped to break down the paradigms that existed at Rolls-Royce in the past, encouraging cross disciplinary team co-ordination: “It means we can comfortably meet with multiple functions and departments, we’re not just constrained to a certain area on the factory floor.
“Now the shop floor operators, all the way through to directors, are engaged in virtual reality and I think it’s very important that everyone is brought through the same journey together.”
Get the full story in the March 2016 edition of Quality World