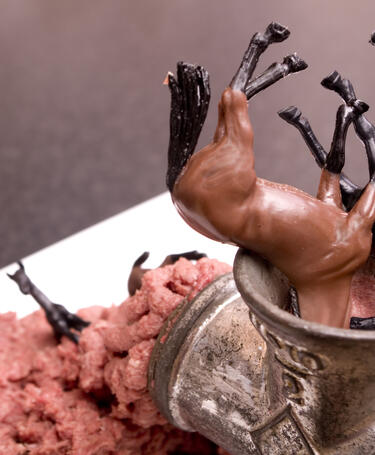
How the horsemeat scandal transformed our supply chain
Progress indicator
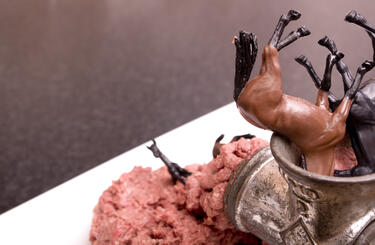
Malcolm Fisher, divisional quality manager at Travis Perkins, describes how the lack of transparency in the food industry helped his team to reconsider its approach to product compliance.
In 2013 the horsemeat scandal shook the food industry to its core, highlighting issues about product quality versus product costs and the lack of transparency in the food supply chain.
Although Travis Perkins works in the building and construction industry, not in the food industry, the scandal enforced the feeling that we cannot afford to be complacent and we decided to review our processes.
My team began to analyse what could go wrong and what additional action could be taken to make sure we continue to remain diligent on product compliance.
An innovative approach
The initial challenge we came across was the large range of 16,000 building and construction products within Travis Perkins. We found testing all the products entering the business would be impractical. Instead we decided to take the approach of raising awareness within the supply chain and working with suppliers on common objectives.
The first step was to create a category product listing to group similar products together and use this to think about what regulations and
standards we need to comply with, as well as any possible risks that could occur.
The next step was to engage the support of Northamptonshire Trading Standards Service as part of the Primary Authority Partnership and Intertek Testing Services, we needed to collaborate and use their experience to continually review and update any risks based on current knowledge.
For example, Chromium IV in leather gloves, used as part of the tannery process, and plasticisers, used in soft grip plastics, both of which are restricted but have the potential to be found in imported products from outside the EU.
Our plan was then communicated to all listed suppliers. The challenge was explaining it was still their responsibility to ensure products are specified and tested for compliance to all appropriate regulations and standards and should be appropriately CE marked as required.
Exceeding expectations
It was vital to treat the additional surveillance review and testing as a way of working more collaboratively with our suppliers, as supply chain transparency is key in preventing any form of scandal. The response has been excellent and suppliers are fully engaged in the programme.
The surveillance testing programme was implemented in October 2015 and I’m really pleased with the results we have seen from the products sampled and tested so far. The level of compliance is very high with no critical failures.
This is an excellent start, not just for gaining assurance that products entering the business are compliant but for raising the profile of quality within Travis Perkins.
So far we have gained positive feedback from a variety of suppliers and internal stakeholders including the commercial teams.
It would be all too easy to relax the testing based on the results but the plan is to continue to use the process to demonstrate Travis Perkins is committed to raise awareness on product compliance and will always have an open-book policy when dealing with the enforcement authorities.