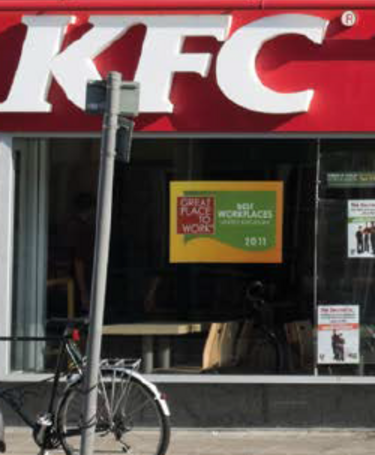
The egg came before the chicken!
Progress indicator
Charlotte Laverty, CQP MCQI, on why the closure of KFC restaurants comes from the chain putting all their eggs in one basket.
It’s been on all the news websites and has been the talk of 2018. KFC has had to close between 562 and 646 fast food chains in the UK because it ran out of chicken. Since this crisis occurred, I have never wanted KFC more in my life. I am amongst the many Brits who are disappointed KFC end clients. When I was having one of my KFC cravings, it got me thinking about how KFC fits into my quality and business continuity role. Surely, this was an obvious risk to the company? The entire context of the organisation is based around fried chicken.
When you start reading further into the articles about the KFC chicken crisis, the cause seems to be shared with DHL, their new distributor. DHL said that “operational issues” meant that several KFC supply deliveries, over the recent days, have been delayed or incomplete. The distributor openly admitted that they made the decision to opt for a new, untested distribution centre with new staff and new technology. This raises further questions about their quality standard, in particular their standards around competence. New staff working at the distribution centre would surely not have the competence required to keep this colossal process running smoothly.
This leads to me wonder, how did KFC control this vital supplier? What criteria was set and how were they evaluated? As determined earlier, the transportation of chicken to the restaurants exposes the company to high risks if anything went wrong. Did KFC audit DHL vigorously before changing suppliers? The innovation in logistics was one of the reasons KFC chose DHL. Wouldn’t this logistics have shown a shortage? Was there a problem with the technology or was the data ignored? The technology should have been audited and tested to ensure it was accurate.
Top management should have created a Risk Register or SWOT and PEST analysis.
In addition to this, DHL only have one distribution centre in the UK for KFC. With regards to business continuity, this should have been flagged as an issue straight away. What would have happened if there was a fire, flood or natural disaster? Or if they ran out of chicken?! These situations should have been tested or thought about to prevent the risks and problems the company found itself in.
I’m not saying that KFC were unaware of this, I just can’t help thinking that it wasn’t thought out very well. Only having one distribution centre would have been a strain at any time. Granted that money is a big part of why business continuity cannot sometimes be done effectively. In hindsight, looking at this situation, running one or two smaller back-up distribution centres would have been far more cost-effective than the millions the company are losing from the closure of its restaurants.
The obvious issue in this chicken shortage crisis is unhappy customers. I believe supply chain management, poorly thought out business continuity plans, and competence and technological factors caused this to spiral out of control. Looking at these areas, there are several things that KFC could have done to avoid these issues, as outlined below:
1. Proper supply chain management
The failure of the supply chain management could have been due to a number of factors. Within KFC, there should have been a centralised, competent team that manages all suppliers. This team should have continuously prompted staff working with the suppliers to review and monitor their performance, reporting findings to the leadership team for further review of the data collated. Going way back to step one of establishing the supply chain management process, a criterion should have been set. This criterion should have taken a risk-based approach, asking the suppliers questions which were core to the business. For example, do you have enough resources, competent staff, etc. The questionnaires should have been reviewed by the team managing the suppliers, ensuring details were on a supplier database and audits carried out if there were any concern. This would not only help the company conform to section 8.4.1 ‘Control of Externally provided processes, products or services’ of the ISO 9001:2015 standard, but also help them manage risks of suppliers. For example, DHL.
2. Solid business continuity
Business continuity is of paramount importance to company of this size. Issues such as the one explained should have been identified and recorded on a Business Impact Assessment. A potential problem of this scale should have been recorded as a major incident, and a plan created. In this plan, you would expect to see items such as how to mitigate risks and business disruption. These mitigation measures could include things such as secondary suppliers.
3. Quality tools
There are many quality tools available which could have been used to help the company. For example, competency matrixes are always beneficial to assess staff competence. Competence is not related to how many qualifications someone has. Granted, training makes up a part of competence, but other factors also need to be considered such as experience, industry knowledge, company knowledge, etc. Creating a matrix that outlines all the items the company believes makes staff members competent, helps give a clear picture of improvement areas, skills within the company, and helps create effective project teams.
Top management should have created a Risk Register or SWOT and PEST analysis. A SWOT and PEST analysis is an extremely useful quality tool which helps leadership to look at the company as a whole. These tools address company Strengths, Weaknesses, Opportunities, and Threats (SWOT) and Political, Economical, Social and Technological (PEST) factors. Looking at these things at a top management level will help the company to record and address areas that need improvement, as well as plan for potential problems, thus ensuring happy customers and smooth operation.
4. What internal and external factors should have been considered?
Carrying on from a SWOT and PEST analysis, internal and external factors should have been considered from a quality and business continuity perspective. Internal factors could have included staff working in the restaurants. With no delivery of chicken, and the closure of many restaurants as a result, staff presence may not have been required at certain branches. Moreover it was the staff that ended up having to deal with unhappy customers.
External factors could have included media, general public, suppliers, vendors, and parent companies. Considering these external factors before the crisis could have helped rectify the problem sooner.
To conclude, I feel this large-scale issue could potentially have been avoided if some quality assurance and business continuity practices had been applied and properly thought about and addressed.
Charlotte Laverty, CQP MCQI, is Quality and Business Continuity Manager at Plusnet
Quality World
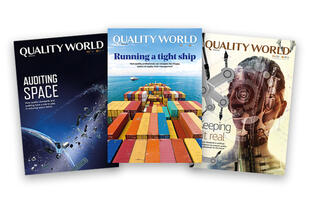
Get the latest news, interviews and features on quality in our industry leading magazine.