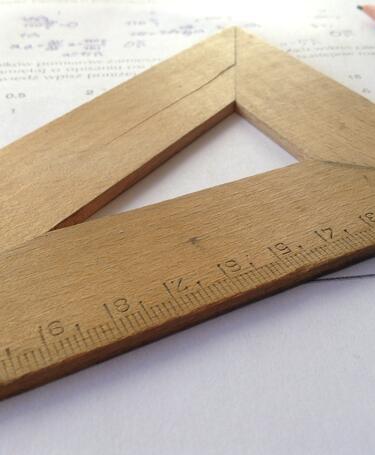
What measures should you be recording?
Progress indicator
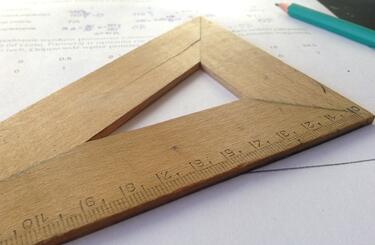
Susannah Clarke, Managing Director at PMI, explores how recording the right measures can help you to improve your processes.
Deciding the right measures to record can be a minefield and we often end up measuring too much, too little or simply the wrong thing. This can lead us to forget the purpose and benefit of measures. Let’s look at the benefits of measures, and the types of measures that will help us improve our processes.
The benefits of using the right measures include:
- The data will inform you about the current process performance
- They are based on your customer requirements
- They help you to learn more about your process
- You can identify the impact of improvements/changes you have made to your processes
- They will signal potential problems.
Measures for improvement and quality
We use many measures in our daily lives outside of the workplace, for example, time and distance apps help us plan our journeys. Doing this is second nature to us.
In our work, we need to use measures for the same reason – we need to know what is going on with our work, so that we can plan accordingly.
There are two measurement categories that help us understand our work processes and to plan – ‘results measures’ and ‘process measures’.
Result measures record the outcomes of the process– The data on the overall process performance which tracks how well you are meeting customer requirements.
Results measures help you identify the processes that need to be improved. However, they won’t give you any clues about where in the process the problems arise. This is why you need to also look at process measures to link any improvements made to the results.

Process measures relate to a process step or sub process.
They indicate where action is needed to improve the performance. For example, task one and task four in a process may have the most mistakes/take the most time/cause the biggest queues or cost the most in manpower.

Once you have your process and process steps, you need to decide the right measure for you to track.
How do you avoid measuring everything or the wrong thing?
It is important to decide your priority measures, the vital few.
Typically, we are interested in three process attributes:
1. Effectiveness – How well the process meets customer requirements
Typical measures include:
- Accuracy
- Reliability
- Ease of use
- Timeliness
- Performance
- Serviceability
- Price/value
- Cosmetics.
2. Efficiency – The amount of resources required to meet customer requirement
Typical measures include:
- Total cycle time
- Processing time
- Waiting time
- Per unit costs
- Rework costs
- Inspection costs.
3. Adaptability – How quickly and easily the process can respond to changing or special customer requirements
- Typical measures include:
- Time to process a special customer request
- Per cent of special requests fulfilled
- Number of approvals needed to meet a special request.
The three attributes of effectiveness, efficiency and adaptability help us understand the priorities for the process and what we need to measure.
At first glance you might be interested in all three but keep your customer in mind to narrow this down. Reflect on what is valued most by your customers.
Finally, now that the vital few results and process measures have been agreed, continuous review of these measures is necessary for this to become a natural part of what you do, how you learn, maintain quality and improve.
The next article from PMI will look at the tools and tips for selecting the correct measures
Quality World
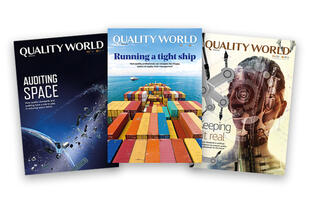
Get the latest news, interviews and features on quality in our industry leading magazine.