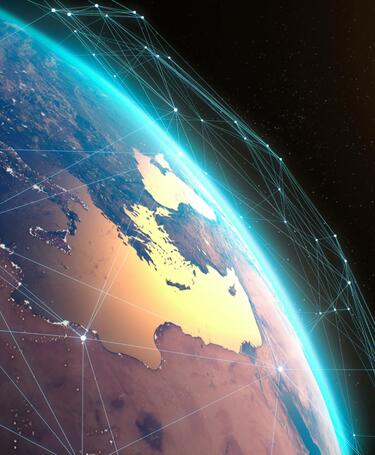
Exploring hidden dimensions – quality culture and cultural quality
Progress indicator
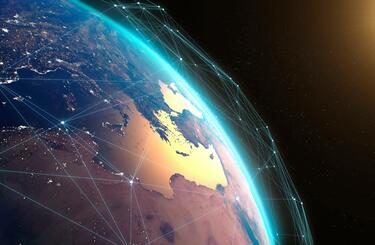
In the first part of a series, Rasoul Aivazi and Richard Brett use stories from their own experiences to explore how Japanese philosophies are intrinsic in quality.
Aivazi is an International Project Quality Lead and a committee member of the CQI Audit SIG, while Brett, now retired, previously had roles as Japan Quality SME and Audit Manager for GSK and is currently Vice-Chair of the Audit SIG.
Ford Motor Company found itself in a unique position in the late 1980s when manufacturing a car model with transmissions sourced from two different origins – Mazda in Japan, and its own factory in the United States.
After the car model's market debut, Ford began receiving requests from customers specifically for the models with the Japanese transmissions. Many even showed a willingness to wait longer just to secure the Japanese variant.
Although both transmissions were built to the same specifications, Ford's engineering team was left scratching their heads over this clear preference for the Japanese version. (The story will be continued in Part 2 of this series, next month).
Such an occurrence sparks thought-provoking questions. Why did this preference emerge? What factors created a noticeable difference in quality between two transmissions of identical specifications? Moreover, how do overarching Japanese philosophies affecting work and life play into such phenomena?
Delving into these questions might reveal the understated yet powerful ways that cultural subtleties shape product quality, influence customer perception and, ultimately, drive business success.
Japan is renowned for its commitment to quality, in both the personal and professional environments. This commitment goes beyond mere performance, it underpins the very fabric of the nation’s culture and ethos. Quality, in the Japanese context, is derived from a complex interweaving of cultural, social and individual values.
This article explores this unconscious cultural influence on quality in Japan, and examines how embracing this quality culture can unleash professional success.
Personal experiences of cultural quality
Story 1: Housekeeping, or the importance of the first impression
I once had the opportunity to join a Japanese quality manager from our company at a quality meeting with a vendor at its factory in Japan.
During the meeting, our manager pointedly asked the factory manager: "If your workshop office is not properly managed and lacks cleanliness, how can you ensure efficient production and overall organisation? How can you manufacture products correctly without proper housekeeping?"
This incident served as a valuable lesson for the factory manager. The next time we visited, the office was immaculately clean and well managed. This time around, the meeting began on a positive note and ended with a successful outcome and satisfaction for everyone.
Story 2: Packaging and wrapping – again, the importance of that first impression
I once worked as a quality manager for a global pharmaceutical company. During my first visit to our Japanese factory, the local quality manager told me that packaging and wrapping are highly rated in Japan. He said: "If you, as the manufacturer, don’t take care over what we can see – the carton, the blister strip, the appearance of the tablet (the 'extrinsic’'quality), how do we know that you will take care over what we can’t see ie, the purity, safety and efficacy of the product (the ‘intrinsic’ quality)?"
This extended, for example, to whether the colour of the cartons was consistent from batch to batch, or whether the container labels were all on straight and at the same level.
This was a very different attitude from that often found in Western cultures where, although the extrinsic quality is important, it is the intrinsic on which we focus.
"I learned a Japanese proverb while working with my Japanese colleagues that emphasises the importance of preparation, stating that 80% of work is in the preparation, with only 20% being the actual execution."
From a Japanese quality perspective, packaging serves as a reflection of the product's quality and value. It is believed that anything well-packaged demonstrates the care and craftsmanship that went into its making. It is seen as a way to express respect for the product and the customer, by creating a positive and memorable impression.
The Japanese also consider packaging a way of enhancing the overall customer experience. They believe that a visually appealing and well-designed container can create a sense of anticipation and excitement for the customer. Opening a beautifully packaged product is seen as an event in itself, adding value and enjoyment to the purchase.
Story 3: Importance of preparation
Years ago, I had the opportunity to represent the quality of the Japanese company I worked for in a major project. It involved a three-day meeting and factory visits to the plants of a major manufacturer in Japan.
During the meeting, our client expressed curiosity about certain project documents. I had anticipated this and prepared the necessary materials in advance, offering them to the meeting to facilitate progress.
This scenario repeated itself three or four times, leading the quality manager from our client’s team to inquire: "How did you manage to prepare all of these in advance?"
My response was simple yet honest: “" came prepared for this meeting." This answer obviously didn’t fully satisfy him, as he continued to probe further, saying: "But your level of preparation is remarkable. These documents, of which we are the owners, were only recently shared with your company. How did you manage to be so well prepared?"
To avoid further inquiries, I told him: "I learned a Japanese proverb while working with my Japanese colleagues that emphasises the importance of preparation; it stated that 80% of work is in the preparation, with only 20% being the actual execution. Ever since I heard it, I have embraced this philosophy and applied it consistently. I approach every meeting with this mindset, including this three-day meeting."
My explanation obviously resonated with him, as he began involving me more in the running of the meeting from that point on.
After returning to his own country, he requested that my company assign me responsibility for the quality coordination of larger orders, not only in Japan, but also in the Far East, Middle East, and EU regions.
This sudden expansion in our scope of work increased our workload and boosted our income substantially.
In summary, I continued working on the project for the subsequent phases, collaborating fully with the client. We successfully managed the equipment for the extension of the project in harmony and trust. Working together, we managed to avoid further potential nonconformities after phase one. As a result, the equipment for the project was released to the site for installation without a single nonconformity.
Our stories about quality and non-quality and customer complaints continue in Part 2 of this series.
Have your say
Share your experiences of quality culture and cultural quality – what lessons have you learned?
Quality Careers Hub
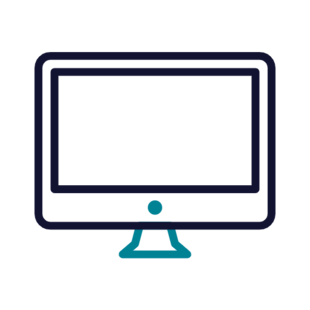
Exclusively for members, the CQI’s Quality Careers Hub is designed for every career stage. So whether you’re just starting out, ready to move on or up, or looking to build on your experience, there are many ways to progress.