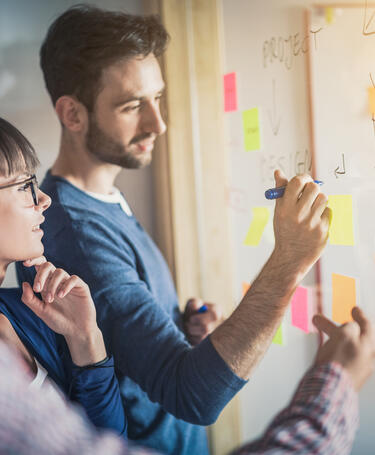
Creating sustainable change when implementing improvements
Progress indicator
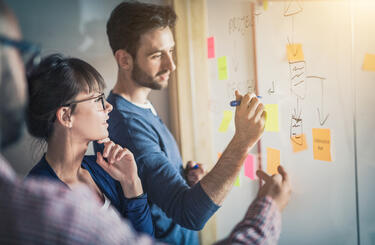
Dave Droar, CQP MCQI, shares his insight on the common challenges of creating positive change.
What are your top tips for implementing an improvement programme that creates sustainable results?
When implementing an improvement programme you need to have what we call a north star. Having clear direction allows you to prioritise and select ideas. You should also have an understanding of where you are currently. Sometimes, even if people have been working together for years, it’s surprising how little they understand about what it is the team does on a day-to-day basis.
The Deming Cycle (also known as plan, do, check, act); Define, Measure, Analyse, Improve and control (DMAIC); and the Lean Six Sigma methodology to record things in a transparent and accessible way, are all useful methodologies for improvement.
It’s also useful to have informal structures to support people such as stand-up discussions on improvement and delegating improvement champions within individual teams. These champions could be trained in quality methods to support and coordinate the focus on a specific improvement activity. These supporting structures can help accelerate ideas to get you from where you are now to where you want to be in the future.
How do you manage improvement when too many changes are happening at the same time?
This problem can arise because a team doesn’t have organisational capability – they can’t physically coordinate or manage change effectively. It can be a capacity issue. The team can be aware of what they’re doing but may not have the time or resources. It could also be an individual issue where he or she doesn’t have the knowledge or skills necessary to carry out a project.
Another problem could be a lack effective prioritisation. In that case, the team has to determine what is most important and how it aligns with the organisation’s strategy. They should ask how it fits with the budget, does it have the greatest impact for the minimum cost? The approach an organisation takes to deal with changes depends on how experienced they are at delivering change or delivering improvement processes. If it is an inexperienced organisation, it may be new or ad hoc. I’ve worked in environments like that and had an opportunistic mindset to get things done. For example, if someone was working on changing the design of the lorry, they could also be asked to make other changes to the vehicle to save time. It was purely done on relationships and opportunism. If the organisation is more experienced, then they could consider breaking projects down in smaller chunks to ensure a higher number of smaller improvements are made.
Irrespective of where your organisation is, all of these require good communications and transparency of what’s going on between the different kinds of traditional areas or silos of your business. It starts with transparency, giving different views of the information to different audiences.
How do you integrate improvement within business risks?
Consider that a risk is any kind of unforeseen outcome. The job of management is to manage variation. As you start to improve a system, the first thing that you do is reduce the variation, and standardise the process. Now it could be that the process is not very good or very efficient or that it doesn’t produce a particularly desirable outcome, but by standardising it, typically what you achieve is a leap in customer satisfaction because you get reliability.
For example, I frequently commute via train from London and it was often late, but late by an unpredictable amount of time. So, my customer requirement wasn’t even on time, but even if it had just been late by a reliable amount that would have been a huge step forwards as far as I was concerned. So even if they just standardised their thought process that would have been helpful.
Once you’ve standardised a processes, if you can imagine that a line that has gone up and down quite a lot and would start to get flat, then you can use that predictability to begin to say: “Well, if I make this particular improvement then I’ve got a reasonable sort of chance that it will have this sort of outcome,” and so you start to make improvements.
Of course, it might be that one of the things that you’re trying to improve is an added risk that the organisation is exposed to. But risk reduction, of course, could be one of the strategic aims. So, I think in both of those regards, that’s how you integrate improvements with risk, one of which is in reducing this kind of unforeseen outcome, reducing the variation through standardisation and one of which is in using improvement once you’ve got a more predictable system.
How should quality professionals deal with resistance from senior management?
My personal experience of dealing with resistance from senior management is to try, as I suppose with any potential conflict situation, to move towards and gauge and understand the motivation behind it. I’ve never met anybody who doesn’t want to do something that’s good for them and, of course, we believe as quality professionals that what we have to offer is of benefit to the senior management that we’re trying to serve.
I’ve discovered that quality is one of those words which is frequently misunderstood because people assume what it means is inspection, cost, bureaucracy and difficulties, whereas actually what it means is stripping out waste and making everybody’s life easier, but I don’t think that’s necessarily the traditional view that people take.
Quality World
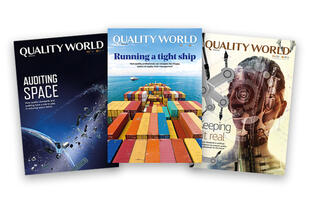
Get the latest news, interviews and features on quality in our industry leading magazine.