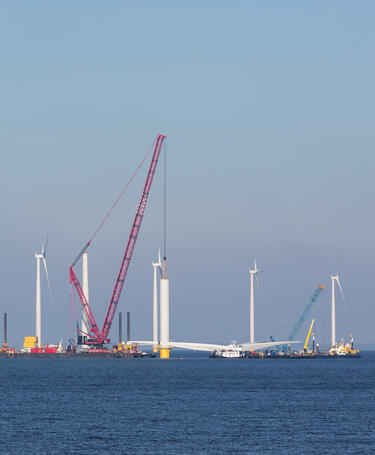
Seacat’s smooth sailing to ISO 9001:2015 and ISO 14001:2015
Progress indicator
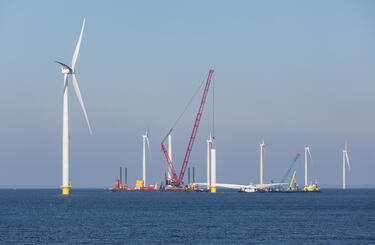
When transitioning to these standards, this operator of wind farm support vessels created systems that go beyond mere compliance.
Based on the Isle of Wight, Seacat Services operates a fleet of 14 support vessels for offshore wind farms in seas across Northern Europe.
Working at sea and dealing with heavy infrastructure means quality and environmental management are crucial to Seacat’s business. Earlier this year, the company became one of the first of its kind to be certified to the 2015 versions of ISO standards 9001 and 14001 for its quality and environmental management systems, with an audit performed by DNV GL.
Hundreds of thousands of companies around the world use these standards, and are required to transition from the 2008 versions to the 2015 versions by September this year.
For Mark Drew, Seacat’s Head of Business Support, making the transition successfully meant first developing an understanding of the new standards, and their updated structure and content. Key aspects of the newly revised standards include understanding an organisation’s context (everything from the market it operates in to how it interacts with its community) and the idea of “risk-based thinking”, which replaces “preventive action” in the new standards, and encourages users to consider risks and opportunities more broadly in their processes and controls.
In this respect, Seacat had a headstart because it already adheres to the International Safety Management (ISM) Code for safety at sea, which employs a similar risk-based approach.
Drew says: “I created a gap analysis of where our system covered each of the points of each of these standards and then saw where the holes were, and did my best to plug them, without feeling like it was just another piece being bolted on, but that it was actually part of an integrated system.”
Then, he says, came “the really difficult bit” which was making sure everybody in the company understood what the standards require. “Softer” areas like organisational context have been particularly challenging to get across, says Drew. But as part of its internal audit process, Seacat took the opportunity to educate staff on these new aspects. “I think we’re there now,” he says.
Quality is embedded in the system rather than relying on somebody interpreting our policy
Respect for the importance of quality has always run through the business. Drew says: “We try and have an ethos that comes from quality and safety throughout the business. It starts with training. When people first come on board, they have a multistep training process which most of them haven’t seen anywhere else before, and that lays out our expectations for how things should be done and the way the management system works as a whole. Then it’s a question of monitoring via KPI (key performance indicator) measures, and when the KPI measures don’t stack up, the key element – and I think the one where the most difficulty lies for most people – is the feedback loop. When things aren’t up to the standard, we need to feed back and work out how to change things to bring it up to standard. It’s difficult, because you need very strong soft skills to deliver the message without making people just dig in their heels and say, we can do things our own way.”
Naturally, the company has a quality policy, but Drew says it takes more than this to make sure that quality is really valued in its culture. “A lot of companies would point to their quality policy and say, this is how everyone here knows about quality.” At Seacat, he says, “quality is embedded in the system rather than relying on somebody interpreting our policy.”
During the transition to ISO 9001:2015 and ISO 14001:2015, Drew created a “compliance table” where each of the standards was cross-referenced with each element of the management system. This, he says, turned out to be a crucial tool which he would have been “lost” without. “Having an overall map of compliance helped make sure the right things are grouped together. It gave me that helicopter view, to check that everything was there and in the right place. “
The aim is for the systems to be “usable, not just compliant”, says Drew. ”You can create a system that’s compliant relatively easily, but to make one that’s useful to the end user, so that they can understand it and find their way around it, that’s the trick.”
On the whole, Drew is a big advocate of the newly revised ISO standards. “I think they’re much more structured,” he says, “they fit together better, so if you’re running more than one, life is so much simpler. We’re doing the ISO 45001 transition probably late this year, and that higher-level structure and risk-based approach being the same makes a huge difference. We’re only a small company, so it’s quite a lot of work to get these things through, but I am keen to get on to ISO 45001, it will help pull everything together.”
Quality World
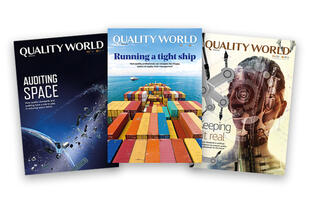
Get the latest news, interviews and features on quality in our industry leading magazine.