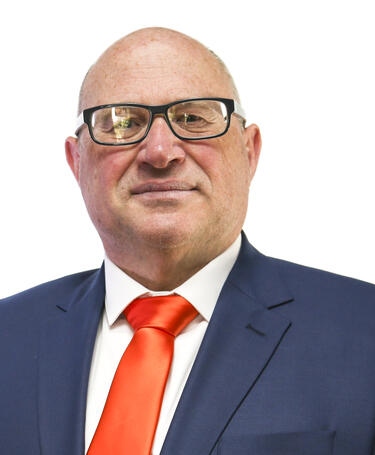
Getting on the right flight path for quality
Progress indicator
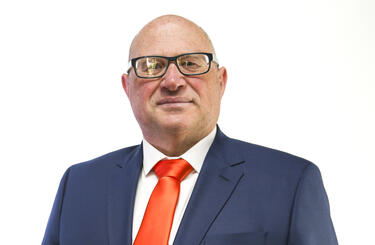
After 30 years as an engineer in the Royal Air Force, followed by 15 years in engineering and quality, Dr Tony Kenneson-Adams reflects on how the RAF’s approach to quality can be applied in civilian life
In the high-stakes world of the Royal Air Force, where 'right first time' is not just a mantra but a way of life, quality is not just a standard or a standard operating procedure. It is an imperative, woven into the fabric of who we are and how we operate; ingrained and intrinsic to daily culture.
From my early days as a 17-year-old aircraft mechanic, throughout my journey to eventually become an Engineering Squadron Commander and aircraft engineering authority, quality was paramount in the Royal Air Force. It was not merely a checklist or a process to conform to; it was what drove the critical necessity of flight safety and mission criticality.
Here, I aim to extract three key lessons from my military experience to show how I choose to bring that same focus to my civilian practice, and share a few quality culture leadership lessons.
While the military context often carries higher stakes, the core question arises: what differentiates military personnel from their civilian counterparts?
At their core, service personnel are ordinary people who choose to wear a uniform and who then do extraordinary things. Civilians can also do extraordinary things, so what can the civilian world learn about the RAF world of quality and so replicate RAF-type results?
I offer these three observations – training, communication, and commitment – to build a quality culture.
Training
As a young airman, I learned the discipline of precision required in every action. Posted firstly to RAF Lyneham, my initial tasks seemed simple – anti-collision light and leading-edge heating and thermostatic controls servicing. However, in hindsight, the importance of quality, even in these simple tasks, was critical to flight safety.
As a 17-year-old, I was entrusted with these responsibilities, subject to final functional test by my corporal. However, I was trusted with the quality of my work that was now hidden under each panel or cover.
Advancing through to corporal, I shouldered increasing complexity in my responsibilities – from cabin pressure control units and pitot-static instrument servicing to supervision of others for maintenance of aircraft components from generators to flight control actuators. These tasks were carried out for peace and war operations, including modifications on the Vulcan bomber that denied Argentinian forces the use of the runway during the Falklands War.
When I think now of the responsibility entrusted to a then-19 to 21-year-old, it seems immense. However, it was as a product of training and a quality culture.
Now that I am a consultant, I find that training in civilian companies can – when compared with that in military life – range from poor to none, often relying more on osmosis than policy. However, I have found time and again that when focused training is introduced participatively and intelligently, teams never fail to rise to the challenge and quality improves.
"The lessons I learned from the RAF's unwavering commitment to quality have served me as a blueprint for replicating an inclusive quality culture in civilian operations."
Training is not an option. You cannot expect to maintain quality and build a culture of quality if leaders do not produce tailored training programmes for each mechanic, technician, pipe fitter, electrician, and so on. A mechanic of 25 years’ experience, who does not understand the relationship between torque and compressive force will never understand ‘why’ every bolt on production equipment needs to have the right wet or dry torque, or why his torque wrench should be calibrated and not used as an additional ‘hammer’.
Communication
One vital lesson ingrained in military culture is the importance of speaking up when something is amiss. The emphasis on open communication channels, and the confidence to voice concerns without fear of retribution, is a cornerstone of the RAF's success in maintaining engineering quality standards.
This practice ensures that potential issues are addressed early and proactively, preventing them from snowballing into larger, more damaging and costly problems.
In the civilian sector, fostering a similar culture of open communication is essential. Employees at all levels should feel empowered to flag quality concerns without hesitation, creating an environment where feedback is valued and acted upon.
It is becoming popular to talk about emotional intelligence and psychological safety in industry; my position is that the application of these must be a priority that is critical to a quality culture.
Commitment
One glaring difference in the RAF compared with civilian manufacturing was the absence of a dedicated RAF quality manager or quality department. Instead, a culture of individual and collective commitment to quality permeated every rank and role.
Whether you were a junior mechanic, a seasoned Senior NCO, or an officer, the expectation was the same: right first time, every time. People are trusted to work with the minimum of supervision; that trust, earned through rigorous training, yes, but practised in a shared commitment to a quality product.
In contrast, the civilian manufacturing plants I encounter are often staffed with quality managers, supervisors, technicians, and a multitude of checks and audits. And yet, poor quality persists, necessitating additional personnel dedicated to handling a constant stream of root cause problem solving (RCPS) and customer complaints. Everyone must be committed to quality through being part of a culture of quality.
Conclusion
In my experience, the RAF’s approach to quality extends beyond the traditional civilian confines of a quality manager and quality department. Quality is a cultural mindset, and an individual and collective commitment.
The transition from civilian quality management to an RAF-style quality culture reveals a stark contrast, but it also presents an opportunity for the civilian sector to learn and adapt.
By instilling a culture of collective responsibility, fostering open communication, and trusting well-trained personnel, businesses elevate their quality standards and safeguard their reputations and success. When each member of the team is a force multiplier for mission/business success then defects decrease, profitability increases and, importantly, reputation and quality grow.
I have seen this journey replicated in many civilian manufacturing plants. When leadership takes charge and moves ahead with training, communication and cultural transformation, they build quality cultures every time.
The lessons I learned from the RAF's unwavering commitment to quality have served me as a blueprint for replicating an inclusive quality culture in civilian operations. It just takes training, communication and commitment.
Why military veterans make good auditors
Mark Walsh CQP MCQI, Technical Director at Q-SYS Solutions, argues that a military background can be an asset for auditing.
Quality World
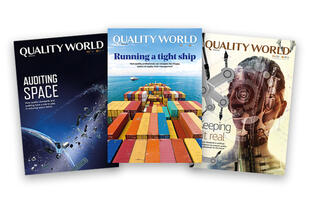
Get the latest news, interviews and features on quality in our industry leading magazine.
Quality Careers Hub
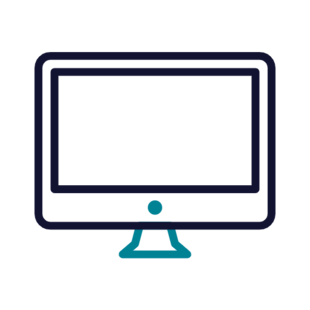
Exclusively for members, the CQI’s Quality Careers Hub is designed for every career stage. So whether you’re just starting out, ready to move on or up, or looking to build on your experience, there are many ways to progress.