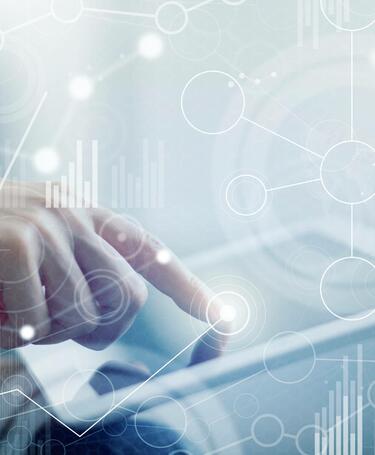
Learning laboratory
Progress indicator
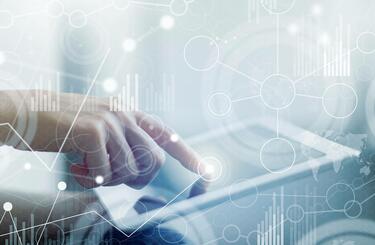
Abdul Majeed PCQI, Quality Assurance Manager at Pragati Electricals in India, describes his experience of the process of gaining certification to ISO/IEC 17025.
The laboratory where I work was required to get accredited and audited in line with ISO/IEC 17025:2017 General requirements for the competence of testing and calibration laboratories. This was necessary to receive clearance approval from the organisations to which we supply the high-voltage instrument transformers we make. Our products were technically in order, as per the relevant standard IEC 61869-1, 2 and 3, but our customers wanted this additional accreditation for the testing laboratory.
Our management team proposed earning accreditation at our laboratory for the testing of instrument transformers. As part of this, I had to undergo training and pass the compulsory examination to become a quality manager of such a laboratory. Other laboratory personnel involved in testing these instruments underwent training too.
Performing a lab audit
As well as the professional behaviour, auditing skills and good understanding of the standard that one would expect of an auditor, they should also have relevant technical knowledge of laboratory management audits when dealing with ISO/IEC 17025:2017.
The lab auditors we had were independent, impartial, observant, perceptive, and focused on assessing the compliance of testing processes, procedures and documented information against specific audit criteria. They interacted with me about each and every test and its importance to declaring the product fit for purpose.
The lab audit was process- and performance-based, and used suitable techniques to collect and verify supplied information, document observations, and record audit findings against technical audit criteria. The auditors were assessing whether the laboratory’s risk-based approach produces valid results for customers and meets ISO/IEC 17025 requirements for technical competence.
Auditing techniques included use of checklists, document review, questioning and listening during interviews, and witnessing activities. The findings were then confirmed by the auditor as either conforming or nonconforming activities.
It is worth noting that in-person audits are more suitable for laboratory audits, although they can be adapted for remote audits. Whether remote or on site, technical audits such as these should be interactive, to allow the auditor to engage with the auditees and develop an understanding of the critical technical issues at hand.
"Because of this accreditation, we have received 25-30% more approvals to supply our instrument transformers, as well as appreciation from our end users."
The audit activities were done based on the scope of the laboratory – for example, the list of tests the laboratory can conduct, its objectives, and its operational activities available for assessment.
A positive audit culture is essential to ensure that technical audits are effective, and I encouraged an open, fair and collaborative discussion between technical auditors and all my lab staff. The technical and lead assessors/auditors clearly communicated with the auditee so that gaps were identified together, which meant improvements could be made to the laboratory processes.
It took the auditors two days to witness the tests and cover all technical clauses. The timeframe was based on risk, the size of the laboratory, and the scope of accredited tests.
Checklists for performing a laboratory audit
The auditors used checklists and software provided by the accreditation body, and they recorded the data and objective evidence against the audit criteria. In turn, the laboratory documented the auditor’s observations, audit findings and records supplied during the audit. These confirmed the findings as compliant or noncompliant against the audit criteria.
The auditors then discussed the noncompliant findings with the team and raised nonconformances (NC) using the agreed processes and format.
Important audit learning points
During the audit, technical staff learned the importance of keeping the laboratory activities impartial. To do this, I developed a reporting method and procedure to avoid clashing with the work of the marketing department. We had to show how we maintained confidentiality around our results, as well as around information created and obtained during laboratory activities.
The auditors checked everyone’s qualifications against the audit criteria and their technical competence in testing the instrument transformers. We were asked to demonstrate the sampling and handling of test objects, so we showed the auditors how it is done by using the proper lifting equipment, cranes and panel trucks. This is a crucial activity, because improper handling could lead to breakages, cracking, contamination or splintering of our samples.
We had to strictly apply methods of tests as per national and international standards, such as IEC 61869-1, 2 and 3 and IS (Indian Standard) 16227-1, 2 and 3.
I also showed the auditors our internal quality control procedures and acceptability of quality control results such as Z-score results (for a test laboratory we maintain less than +/-2), and the intermediate check results.
As a quality manager, it is very important to consider the uncertainty of measurement and environmental conditions when declaring the results. I had to test and show that the capacitance and dielectric dissipation factor test is affected by humidity and temperature, and earthing of the test equipment.
Outcome
The auditors suggested we make a record of every nonconformance raised during the audit and analyse whether that nonconforming work had led to changes in the test results. This suggestion has been very useful to me, as it has given me a kind of chart by which to monitor my laboratory activities.
The accreditation to ISO/IEC 17025:2017 gave our laboratory an edge over our competitors by enhancing confidence in our test results. Because of this accreditation, we have received 25-30% more approvals to supply our instrument transformers, as well as appreciation from our end users. We have also enhanced our export scope and have gained more export orders.
Read more great content from Abdul Majeed
There are lessons to be learned during an audit, outside of the formal process. Abdul Majeed, Quality Assurance Manager at Pragati Electricals Pvt. Ltd in India, makes the case for learning over lunch.
Become an event partner for Quality Live 2025
Raise your organisation's profile with our audience of international quality and auditing professionals
The latest from the CQI Podcast
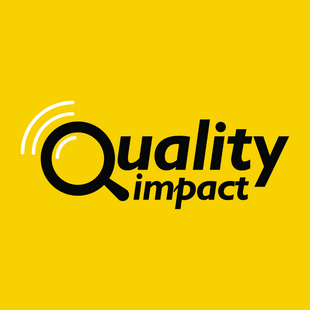
Listen to the Quality Impact podcast, where experts share insights on the evolving role of quality across industries.
Quality World
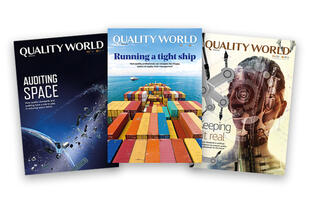
Get the latest news, interviews and features on quality in our industry leading magazine.