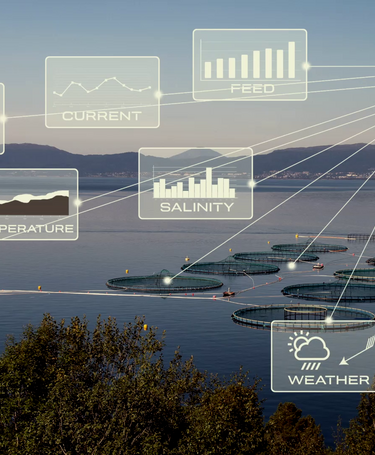
Management systems in the digital age
Progress indicator
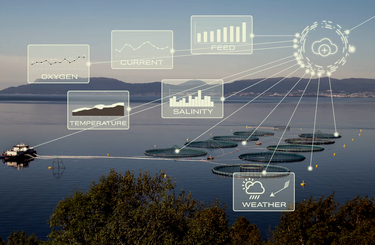
DNV GL is the headline sponsor of the CQI’s inaugural International Quality Awards. Shahram G. Maralani, global director of technology and services, explains how digitalisation impacts the work of quality professionals today.
How can quality professionals prepare for the future?
Quality professionals need to stay fit. Historically the world has moved from craftsmanship to mass production, which was when we introduced quality control. When the production capacity increased, we moved to quality assurance and later to wider quality management. Today, one of the main trends in business is digitalisation. Quality professionals need to consider what that demands in terms of how we manage quality, safety, environmental assurance and the assurance of other related aspects of the business. Quality professionals need to speak the business language and with a digital accent.
How will quality professionals have to change the way they look at management systems?
Consider the speed and accessibility of data in today’s quality management systems. Take customer satisfaction process for example. If you search online, you can find a lot of information on how satisfied customers of an organization are without knowing that organisation intimately. Another example would be the ability of combined sensors connected to analytical dashboards that show live data and analysis on performance of a process in real-time. Traditionally, the information would be made available through manual reporting once every six or twelve months during an audit. Real-time access to performance of systems gives improvement possibilities beyond imagination. Hence, there is a necessity for quality professionals to think outside of the box – outside of the traditional assessments limited to processes.
The digitalisation era that we are living in is often called Industry 4.0, as is considered a new industrial revolution. Developing new areas of expertise in digital management is mandatory for quality professionals navigating in today’s business landscape.
Today, quality professionals look at the past when they go out to audit. Will this also change?
I think we will continue to look to the past. You always need to have a reference in mind, especially if you use the continual improvement cycle. You should compare the new results with your original plan, which is the check part of the continual improvement cycle.
What is new is that we have particular parameters and various data sources, some of which we can’t yet even determine if they have any correlation with the problem we are trying to solve.
Let me share a story that you can find on some literature about the topic. Several store clerks noticed that men often bought beer at the same time as they bought diapers. The store mined its receipts and proved the clerks' observations correct. So, the store began stocking diapers next to the beer coolers, and sales skyrocketed. The story is a myth, but it shows how data mining seeks to understand the relationship between different actions and enables us to plan or predict the future. It’s about making sense of the data we don’t necessarily understand. Quality professionals must become competent in understanding data and analytics further, planning and improving the future by understanding the past.
Could you talk about your experience of digitalisation so far?
My background is in mechanical engineering, automotive industry and management. I have also done some software programming during my educations and previous work experience. I have always been interested in information and communication technology and following evolving trends. Hence, understanding and making the most out of the digitalisation revolution comes natural. As quality and management professionals, it is important for us to understand if there are technologies that can make evolution or even (at least small) revolutions in the way we manage our processes.
In DNV GL, we are well into our digitalisation journey. In November 2017, we launched a platform called Veracity (veracity.com). It serves as an open industry data platform and a marketplace for services in various industries. We call it an eco-system, built to help us and our customers create value out of data. This is one of the initiatives we are taking to address the needs of organisations, and provide assurance in a digital world.
When it comes to management systems, we have been thinking of opportunities to innovate the digitalisation of management systems. Around two years ago, we launched LuminaTM, a performance benchmarking tool. Here, we use the data we collect through management systems audits to create more insight for our customers. Today, in our database we have close to two million findings. We use anonymous information from these findings to do analytical studies. For example, you can compare the trends experienced by different industries, or compare different geographies in the same industry and so on. In this way, we have innovated the way we provide value through management system assessment. The first step is to look at how we can use the digital possibilities in a management systems framework.
The latest digitalisation move was to move all our management systems, products and supply chain certificates to be stored and updated in a secure private blockchain, allowing anyone to obtain instant confirmation that a certificate is valid and up to date. We are the first in our industry to do this.
How would you define blockchain?
A traditional way of storing almost any type of transaction is by storing it in a central ledger. In blockchain, you put these transactions in an open, distributed ledger. By comparing these copies (which could number a hundred, five hundred, a thousand, or more depending on how many nodes you have in this network) you can ensure trustworthiness of the data.
We have put all our certificates in the blockchain. What the customer or their stakeholders see is a QR code on the certificate. The QR code provides access to registered information in the blockchain, such as the scope, the name of company and validity of certificate information.
Why is digitalisation an important issue for quality professionals today?
The boundaries between the physical world, which includes the assets and products within the scope of a management system, and their digital twins is getting less observable. The more this happens in the industry, the more it will be difficult to design, build, assess and assure a quality system in the future without having this digital know-how. Development on this will be faster in some industries and may be a little bit slower in others. This is what’s driving the necessity for quality professionals to start educating themselves in digitalisation.
Could you clarify what you mean by digital twin?
Imagine you made a very expensive investment to build a new vessel or a new oil platform and want a way to test certain criteria before starting the detailed design. You can create a computer simulation or a model so that you can test ideas on a digital copy of the asset, which has not been built.
If you want to see what will happen if you change the temperature by two degrees in a high-risk installation, you can do it on the digital model instead of the real thing. It would be costly or impossible to test such scenarios on a physical installation. Technology enables us to simulate reality and make better evaluations and decisions.
The concept of simulation and modeling is not new. What is new is the ability to use multitude of data from real or virtual sources in modeling the real product or asset in a virtual or augmented environment.
Could you talk about the benefits of digitalisation?
I’ll give you an example. Today, an electronic chip manufacturer has a website where you can see the environmental aspects of the whole plant, live. This could be information on how much the plant is emitting to the sky, how much it is impacting the temperature of the surroundings, how much energy the plant consumes or the amounts and specs of its water discharge. Access to this live information isn’t a replacement for an assessor. But if all this data is augmented, there’s a potential to make an assessment more focused, data-driven and more to the point. This data could also be used for the benefit of the community near the plant. The houses around the factory can be proactive stakeholders in their neighbourhood environment. In this way, digitalisation also caters higher transparency, which is a valued quality within assurance.
What are the challenges that come with the digitalised management system?
Newton’s third law of motion states that there’s always a reaction towards any action in the world. As we think about the digitalisation of the world and the impact of the management systems, there may be less need for a physical audit. Our profession would need to evolve.
The first challenge is to re-educate the quality professionals of today in a cross-discipline framework.
The second would be rewriting standards fast enough to keep up with the changes that are happening. I would assume that international standards, like the ISO standards on management systems, need to adjust. Data has a big role to play in assurance and auditing of the management system. Today’s management system is dependent mostly on auditors and the information they collect through the company’s systems. Tomorrow, this data can come from more sources. And do not forget technology leapfrog. It may happen in all geographies, faster, wider and deeper than we could believe.
Thirdly, the management system of the future may have challenges with data sharing and data ownership. If the digital assurance world becomes a reality, there will always be these types of discussions around who should have access to the data.
The fourth challenge is cybersecurity. Hackers across the world orchestrate attempts to shut down an industry or even attack a nation. If supply chains are compromised, hackers could decide how a supply chain node is prioritised. This could have a direct impact on the stock price of a supplier or sustainable supply of goods.
What advice do you have for quality professionals working to adapt to this change?
The first one is to stay curious and to stay tuned. The evolution of quality and other management systems may come from somewhere that you don’t even imagine. It may not come from the traditional designers of the framework of management systems, maybe somebody else can disrupt and come up with an idea that totally reshapes management systems and their assurance.
At the same time, it is wrong if we think that what we do today will become irrelevant. We should not leave the legacy of management systems behind, but we should learn about the future at the same time. We should try to find out how we, as consultants or as assessors of management systems, can benefit from new technologies and from the new sources of data available to do our job better, leaner, easier and faster.
Wherever we live, we should challenge our peers in national standard bodies and other standard setters about their digital assurance roadmap. We should enable the journey of evolving into a digital age of assuring compliance and performance.
How do you see the future of management systems?
If you look some years back, the digitalisation of management systems was to create less papers. We moved from paper-based systems into PDF (or equivalent) files. I think the way forward we will see less PDF files. Requirements and design of the system will be more and more built into the companies’ systems where assurance is also digitally enabled. Hence digitalisation is one side of this future.
On the other hand, today, you have different streams to assuring products, processes and management systems. There will be a much closer link between process and products. At the end of the day, the demands and expectations of customers and stakeholders are what matter most. The end user or the professional user does not differentiate between processes or products. They care about their overall experience and the quality of that experience. Thus, evolution of the scope and framework of assurance is the other dimension in the future of management systems.
As in all industries, we will see a higher degree of digitalisation and automatization. The digital era changes business all over the world. Management systems are integrated into the way organizations do business, hence they will and must adapt accordingly.
I think we are in the beginning of the digitalisation of assurance. There’s much we don’t know. We all will need to learn and adapt to this evolutionary and potentially revolutionary process.
Blockchain certificates
DNV GL uses a decentralised database or “digital ledger” to keep information secure
International Quality Awards
The awards celebrate quality professionals who have made an exceptional impact in their organisations. Meet the winners.
Quality World
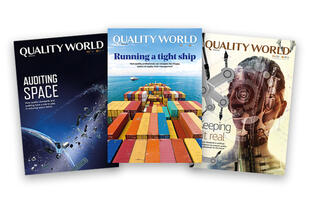
Get the latest news, interviews and features on quality in our industry leading magazine.