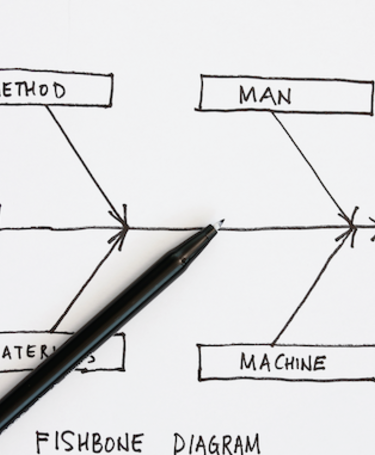
Quality tool: Cause and effect diagram
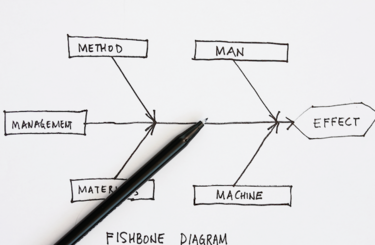
Richard Green, CQP FCQI, Director of Kingsford Consultancy Services, UK, takes us through the Cause and Effect Diagram and how to apply the tool correctly.
What is it?
The Cause-and-effect diagram – also known as an Ishikawa, fishbone or Fishikawa diagram, is used to identify the potential causes of a specific event, known as ‘the effect’. Based on brainstorming, the technique provides a way of rationally determining and organising the factors that are suspected of contributing to the effect. These must then be tested and verified. Corrective and preventive actions can then be applied to mitigate or eliminate relevant factors.
When and how can I use it?
Cause-and-effect diagrams are commonly used in product design and quality defect prevention, but they can also be used in any situation where an understanding of the root cause of a problem is required. The analysis is best conducted between groups of individuals with a shared understanding of the nature of the issue under examination. Each group should then be able to add their own perspective to the analysis.
Steps on applying the tool
1. Clearly define the effect to be explored.
2. Draw the backbone of the diagram running horizontally from this definition.
3. Brainstorm the likely major categories of causes of the effect and add these as spines coming out from the backbone.
4. Brainstorm all the possible causes of the effect. Ask: "Why does this happen?" and write each idea on the appropriate spine(s).
5. For each identified cause, ask: "Why might this happen?" , then write down the possible sub-causes branching off the causes.
6. Continue to ask "Why?" and generate further levels of sub-clauses causes.
7. Keep going until the ideas are exhausted.
Example
Typical major categories in the manufacturing sector might include: Man, Machine, Methods, Measurement, Materials, and Mother Nature (Environment). In this example, a light engineering company has applied cause and effect in an attempt to identify the reasons why it continues to produce poor quality parts. It has taken the 6Ms suggested for manufacturing and the results of their brainstorm are as follows.
Causes identified include, amongst others, a failure to train staff, the use of old technology, insufficient budget for calibration and insufficient staff resource in the purchasing department. For each of these, further ‘why’s?’ could be asked to dive deeper.
Did you know?
During World War Two, there was a rumour circulating in Japan that Ichiro Ishikawa originated the Fishbone Diagram in 1943. However, many reports published after this date claim it was his son Professor Kaoru Ishikawa who created it in the 1960s.
In current times, there is still some uncertainty as to who originally invented the Fishbone Diagram out of the father and son duo.