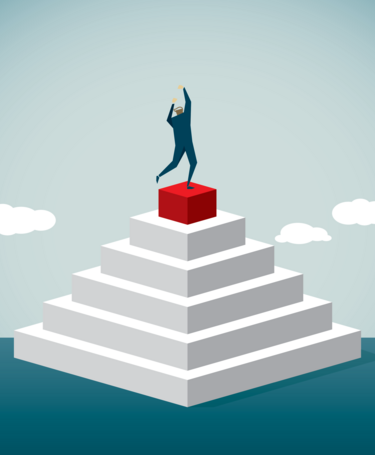
Hierarchy of improvement
Progress indicator
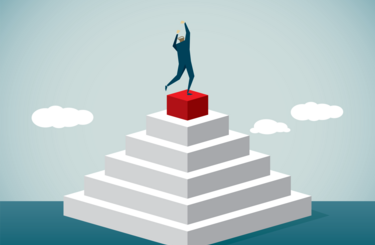
Jessen Yeoh CQP MCQI, an IRCA Principal Auditor and a principal advisor at P Excel Advisory in Melbourne, Australia, draws on ISO 9001 to outline the ‘hierarchy of improvement’.
Every successful organisation has an ongoing focus on improvement to maintain its performance levels, reacting to changes in its internal and external conditions and creating new opportunities (ISO 9000 Clause 2.3.5.1 & 2.3.5.2).
ISO 9001 Clause 10.1 (Improvement – General) requires an organisation to improve its products and services to meet requirements, address future needs and expectations, correct, prevent or reduce undesired effects, and improve the performance and effectiveness of its quality management system.
According to ISO 9000 Clause 3.3.1, improvement is defined as "activity to enhance performance", and can be ordered into six levels:
- correction;
- corrective action;
- continual improvement;
- breakthrough change;
- innovation;
- reorganisation.
I call these six levels of improvement the 'hierarchy of improvement'.
Level one
The lowest level is correction. Correction is an “action to eliminate a detected nonconformity” (ISO 9000 Clause 3.12.3). A correction could be repair, rework, return, regrade, redo etc., which is just a reaction to the nonconformity, or taking action to control and correct the nonconformity, as well as dealing with the consequences (ISO 9001 Clause 10.2.1 (a)). Root causes are not identified and eliminated, and the same nonconformity may happen again in the future.
Level two
As stated in ISO 9000 Clause 3.12.2, corrective action is an "action to eliminate the cause of a nonconformity and to prevent recurrence". An organisation is required to evaluate the need for action to eliminate the causes of the nonconformity so that it does not recur or occur elsewhere.
If necessary, the organisation must update its risks and opportunities register and make changes to its quality management system upon effective implementation of corrective action, as outlined in ISO 9001 Clause 10.2.1 (b) & (f)).
Both correction and corrective action are 'reactive' improvement processes ie, actions will only be initiated if nonconformities, such as customer complaints, defective products and so on, occur. That means if nothing is 'broken' no action will be taken.
Level three
The next level is continual improvement, or 'Kaizen' in Japanese. This is a proactive process and is defined in ISO 9000 Clause 3.3.2 as "recurring activity to enhance performance".
These are incremental or small-step activities using, for instance, quality objectives, monitoring and measurement, internal and external audit findings, to identify opportunities for improvement. ISO 9001 Clause 10.3 (Continual improvement) requires organisations to "continually improve the suitability, adequacy and effectiveness of the quality management system" by considering "the results of analysis and evaluation, and the outputs from management review...".
Level four
Level four is breakthrough change, which is also a proactive improvement process. At this level, an organisation follows a structured approach and applies tools and methodologies such as Lean, Six Sigma, and quality control circles to achieve objectives.
Processes are deployed to implement improvement projects throughout the company. A systematic procedure is developed to monitor the planning, implementation and completion of such schemes.
Level five
Innovation is Level five in the hierarchy of improvement. Changes in an organisational context may require innovation. This is defined as "new or changed object realising or redistributing value" and generally significant in its effect.
An organisation's innovation process should align with its strategic direction. Innovations are not only responding to the changing needs and expectations of interested parties, but also anticipate potential changes in the organisation and in the life cycles of its products and services, as stated in ISO 9004 Clause 11.4.2 (a). Innovation can be applied at all levels of the organisation through changes in technology, products, services, processes, management system and business model.
Level six
The highest level of improvement is re-organisation. Sometimes it may also be called 'business process re-engineering' or 'corporate re-structuring'.
Reorganisation is a process to enhance organisational performance, for example organisational effectiveness, economic efficiency improvement, cost saving and so on, to meet the needs and expectations of interested parties. Reorganisation may come about through changes in a company’s constitution, governance and organisational structures, or its management system or business model eg, digitalisation.
Summary
Level 1 (correction) and Level 2 (corrective action) are reactive improvement processes, while Levels 3 to 6 (continual improvement, breakthrough change, innovation and re-organisation) are proactive processes.
As a basic quality management system standard, ISO 9001 only requires an organisation to demonstrate implementation of Level 1 to Level 3 improvement activities. For instance, correction (ISO 9001 Clause 8.7.1 (a), 9.2.1 (e) and 10.2.1 (a)), corrective action (ISO 9001 Clause 9.2.2 (e), 9.3.2 (c) (4) and 10.2) and continual improvement (ISO 9001 Clause 5.2.1 (d), 7.1.1 and 10.3).
Level 1 to 3 improvements could be initiated, implemented, and maintained from the bottom up in an organisation. However, an "…organization might find it necessary to adopt various forms of improvement…, such as breakthrough change, innovation and re-organization"(ISO 9001 Clause 0.1 General).
Breakthrough change, innovation and re-organisation (Level 4 to 6) must be initiated and led by the top management (a top-down approach) as they involve significant leadership commitment and resources, both human and financial. To cultivate improvement culture in an organisation, engagement of top management in improvement initiatives is essential.
Adopting a business management system
Roy Rogers CQP MCQI explains the process of implementing a new business management system at Enigma Industrial Services
Join the conversation
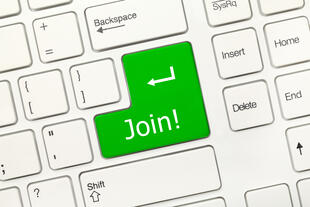
Become a member and you too could input into future revisions of standards such as ISO 9001.
Quality World
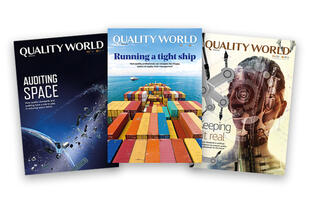
Get the latest news, interviews and features on quality in our industry leading magazine.