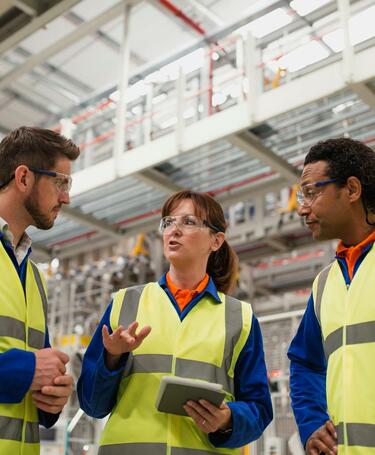
Preventing workplace injuries with hazard identifcation
Progress indicator
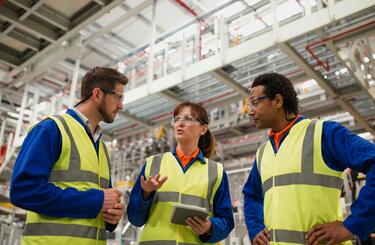
IRCA Principal Auditor Ravindiran Gurusamy outlines a methodology that can be used to identify and prevent health and safety hazards in the workplace.
The burden of occupational injuries and/or diseases is significant for employers and the wider economy, resulting in losses from early retirements, staff absence and rising insurance premiums.
Societal expectations for sustainable development, transparency and accountability have evolved, with increasingly stringent legislation. There has been growing pressure in recent years for organisations to adopt a systematic approach to occupational health and safety management, by implementing ISO 45001:2018 Occupational health and safety management systems – Requirements with guidance for use.
The intended outcome of an occupational health and safety management system (OHSMS) is to provide safe and healthy workplaces, prevent work-related injury and ill health and to continually improve an organisation’s OHSMS performance.
Creating a safety culture
A culture of safety should be created by employees for the benefit of each other. However, occupational health and safety (OHS), like anything, needs to be practised.
Health and safety are cultural pillars in every industry, and it is the primary responsibility of each organisation to take them seriously, for direct employees and other service providers. Consequently, it is critically important for organisations to eliminate hazards and minimise OHS risks by taking effective preventative and protective measures.
In this context, a hazard can be a source, situation or act with a potential for harm in terms of human injury or ill health.
Risk-based thinking enables an organisation first to determine the factors that could cause its processes and management system to deviate from the planned results, and then to put in place preventative controls to minimise negative effects and make maximum use of opportunities as they arise.
PDCA cycle approach
To ensure the continual improvement of an organisation’s OHSMS performance, the Plan, Do, Check, Act (PDCA) cycle approach can be applied.
"Health and safety are cultural pillars in every industry, and it is the primary responsibility of each organisation to take occupational health and safety seriously, for direct employees and other service providers."
Assessment of OHS risks and opportunities, occupational hazards, compliance obligations and objectives are all part of the ‘Plan’ phase of the cycle.
The ‘Do’ stage can include allocation of resources with required skill and competencies, establishing operation controls, as well as hierarchy controls to mitigate the OHS risks, and preparedness to meet emergency situations.
To fulfil the ‘Check’ stage of the cycle, organisations should establish and implement what parameters are to be monitored and measured, in line with its OHS policy, while identifying objectives with appropriate measurement techniques and controls.
Then, the organisation can ‘Act’ to continually improve the organisation’s OHS performance to achieve the intended outcomes of providing safe and healthy workplaces and preventing work-related injury and ill health.
Hazard identification and risk assessment
Every organisation has two potential sources of risks – higher risks from internal and external issues, and the needs and expectations of interested parties; and next-level risks from day-to-day operations that result in assessment of occupational hazards and their associated risks.
To control the occupational hazards and mitigate the risk of Injury and ill health, the systematic risk assessment tool Hierarchy of Controls can be used. The key points of this are as follows.
Elimination: physical removal of the hazard is the most effective hazard control.
Substitution: the second most effective hazard control which can be implemented in the situation where elimination of the hazard is not possible, replace the hazardous process with lower risk process.
Engineering controls: this will enable to isolate the hazard from the personnel. These controls are generally existing where elimination or substitution are not practically possible.
Administrative controls: these controls do not remove the hazards, but significantly reduce the occupational risks by creating more awareness to the team through well established procedures, instructions, sign boards, systematic trainings, and periodical reviews etc.
Personal Protective Equipment (PPEs): PPEs are the most important and generally followed by the majority of the organizations. The success factor depends on the suitability of PPEs to the nature of the occupation, type of the hazard and PPE adherence by the personnel.
Combination of two or more controls will always yield better benefits in terms of reducing the occupational Injury or ill health.
Practical steps
While many organisations may believe that the identification of several hazards and risks show weaknesses in the company, this is not the case. In fact, it underlines the strength of an organisation in demonstrating its commitment towards preventing Injury and ill health of their employees.
As well as identifying the worst, and/or the most likely, risks, discovering hazards in the workplace allows the creation of control measures and the introduction of training programmes to mitigate risks.
The following step-by-step procedures may be applied in identifying hazards in the workplace:
Step 1: activity capturing activities
These can include routine and non-routine activities of all those who have access to the workplace, as well as human factors, new or modified activities, and potential emergency situations.
Step 2: hazard identification
Health and safety hazards could include physical, mental, chemical, biological, mechanical, electrical and psychosocial, and so on. Evaluate each hazard with the applicable local, national, or international legal requirements.
Step 3: risk assessment
Identify probable consequences of the hazards identified in Step 2. Based on the consequences, identify the criteria for the severity of each hazard. From the likelihood and exposure level, one can then derive the risk priority number (RPN). Classify each risk as ‘tolerable’ or ‘intolerable’, based on the RPN and overriding criteria.
Step 4: identify
List the existing controls which are already implemented.
Step 5: implementation and review
Review the implementation of the control measures that are in place to mitigate incidents of intolerable risk. Any proposed risk control measures should reduce the risk, according to the Hierarchy of Controls.
After implementing the controls, reviewing and identifying the residual risk in each activity, operation controls should be established to keep any risks under control.
Once the hazard identification and risk assessment (HIRA) has been established, the intended OHS objectives should be monitored or measured.
The HIRA document should always be kept up to date, and it should be reviewed at defined intervals, which can be superseded in case of a nonconformity. This should also be done with the participation of employees on the shop floor.
It is always better to implement one or more controls individually or in combination to keep the risk as low as reasonably possible.
For example:
Elimination: forklift usage eliminated for material movement from one station to another.
Substitution: roller conveyors being installed for the material movement.
Engineering controls: chain guards, Limit switches, Photo sensors, Overload protection.
Administrative controls: training, safety instructions, warning boards, preventative maintenance plan, and implementation.
Personal protective equipment (PPE): Safety shoes, gloves, goggles.
After implementing the controls, review and identify the residual risk in each activities and establish operation controls to keep the risk under control.
Once the hazard identification and risk assessment (HIRA) has been established, monitor or measure the intended OH&S objectives as applicable and evaluate the actions appropriately. Maintain the HIRA document up to date and keep review at defined interval which can be superseded in case of a nonconformity. The same can be discussed during the consultation and participation of workers.
Summary
A HIRA is one of the best tools for every organisation to use in preventing the occupational related injury and ill health of its employees, demonstrating as it does the OH&S policy commitments and compliance obligations.
Read more from Ravindiran Gurusamy
IRCA Principal Auditor Ravindiran Gurusamy examines the compliance obligations that are required in an environmental management system.