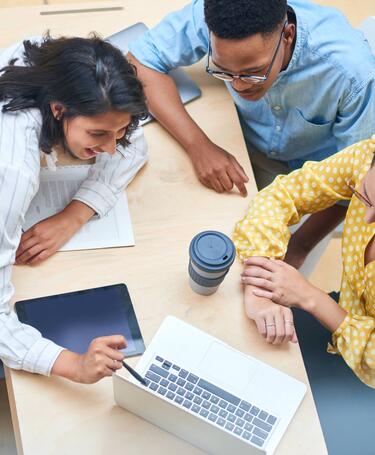
Through the lens of the auditee
Progress indicator
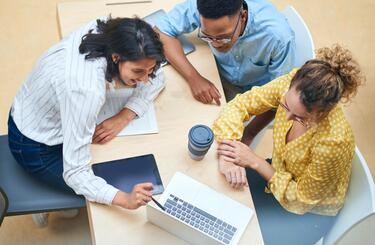
(Ben) Ho Bun Chan CQP MCQI offers audit insight from the other side of the table, examining how an organisation undergoing ISO certification for the first time can get the best out of the process.
Thorpes Joinery is an established company based in Market Harborough, Leicestershire, with decades of experience in delivering joinery manufacturing and installation to clients across different industries. Recently, the business recognised the potential benefits of ISO certification: how to enhance its operational framework, environmental stewardship, and workplace safety standards to secure a competitive edge. Thorpes began its journey to ISO certification in late 2023, for Quality (ISO 9001:2015), Environmental Management (ISO 14001:2015), and Occupational Health and Safety (ISO 45001:2018), and achieved certification in September 2024.
A necessary evolution
Thorpes’ decision to pursue ISO certification stemmed from practical and strategic motivations. The directors recognised that having these globally recognised certifications would give clients greater confidence in the company, as well as simplify the tendering process and future-proof the firm against evolving regulatory and client expectations.
ISO certification is not merely about compliance; it is about creating a foundation for sustainable growth and continuous improvement. The process should begin with a clear understanding that certification is not just a box-ticking exercise; it demands a cultural shift to embrace quality, safety and sustainability as central pillars.
Initial perceptions
Any audit process starts with a degree of apprehension. Will the auditors be overly critical? Will their approach be supportive or confrontational? Will there be any conflicts?
However, what was immediately evident in our initial Stage One audit was that the auditors approached their role as collaborative partners. They focused on identifying areas for improvement, while recognising the organisation’s strengths and how it was conforming to the requirements of the ISO standards. Their ability to explain the standards in a practical, non-technical manner was crucial in demystifying the process.
Preparing for the standards
Aligning with the requirements of ISO 9001, 14001 and 45001 was a comprehensive undertaking. For a joinery business such as Thorpes, it meant evaluating existing policies, reviewing current operations, and preparing documents and evidence. Key areas of focus included:
- Quality management: ensuring robust documentation, clear processes and consistent delivery of high-quality products.
- Environmental: minimising waste, managing energy use and ensuring responsible sourcing of materials.
- Workplace safety: identifying and mitigating hazards, while fostering a safety-first culture among employees.
One of the biggest challenges was balancing the day-to-day demands of production with the preparation required for certification. It was vital to engage employees at all levels, making them active participants in the journey. Regular training sessions, clear communication and celebrating small milestones helped us to maintain momentum. We also had regular meetings with our adviser from Independent Advice for Business to ensure we had an achievable action plan to complete the preparation before the audit.
"The auditors’ ability to foster dialogue rather than interrogation was particularly impactful. Questions were framed to encourage reflection, such as: ‘Can you talk me through how you handle material waste?’"
The audit experience
Taking part in the first audit was an eye-opening experience. The auditors’ structured approach made it clear that they were there to assess how the business conforms to the audit scope and the standards, and it helped us discover opportunities for improvement.
The auditors’ ability to foster dialogue rather than interrogation was particularly impactful. Questions were framed to encourage reflection, such as: “Can you talk me through how you handle material waste?” This not only put employees at ease, but also underscored the practical relevance of the standards to our operations.
As part of the auditee responsible for ISO 9001, I assumed we would have to prepare a lot of paperwork and evidence, policies and documents, etc. This was a lot less stressful than expected. Our business follows a stringent system that made the audit progress much easier and meant we could present the auditors with a well-documented project to demonstrate our compliance.
Lessons learned
Reflecting on the experience, several lessons stand out that could be valuable for other first-time auditees:
- Preparation is key: invest time in understanding the standards and aligning internal processes accordingly. Don’t wait until the last minute.
- Engage the entire team: certification is not just a management responsibility. Everyone in the organisation plays a role.
- View auditors as allies: a collaborative relationship with auditors can transform the process into a learning opportunity.
- Focus on continuous improvement: certification is not the end goal—it’s a stepping stone to ongoing excellence.
Feedback for auditors
From an auditee’s perspective, the best auditors are approachable and communicate well. Not only does this make the auditees less nervous, but it also forms a rapport early in the process. Ideally, the certifying body will match organisations to auditors with similar backgrounds, which helps with communication.
Practical insights and constructive feedback are more valuable than a checklist approach, as we have found our auditor’s advice very helpful.
For businesses new to ISO certification, offering pre-assessment guidance or examples of best practice can make the process less daunting and more engaging. The best thing our auditor did for us was to clearly explain that they were there to assist us with the process by assessing how we conform to the standards.
We also found that when the auditor showed a genuine interest in our business, it helped boost engagement and provided a real opportunity for us to help them understand our company. Ultimately, the audit is a chance for us to showcase and help the auditors understand the nature of our business, and to be open to opportunities for improvement.
Positive impact
Achieving ISO 9001, 14001, and 45001 certifications has transformed how Thorpes Joinery operates. Internally, it has created a more structured and efficient environment, with clear roles and responsibilities. Employees take pride in knowing they are part of a business committed to the international standards in quality, sustainability and safety.
Externally, our clients view the certifications as a mark of credibility and professionalism, which helps to simplify the tendering process. For certain contracts, having ISO certification has exempted us from additional due diligence, giving us a competitive edge. It has also opened doors to new opportunities with clients who are seeking partners that align with their values.
The journey to ISO certification has been transformative for Thorpes Joinery. As we look to the future, maintaining and building upon these certifications will remain a priority, ensuring we continue to deliver the highest standards of quality and service to our clients.
To those considering the journey, our advice is simple: embrace it. The road may be challenging, but the rewards – for your business, your clients and your team – are vital.
Join IRCA
Becoming an IRCA member demonstrates your professional competence to the world. Find out more on how to join.
Quality World
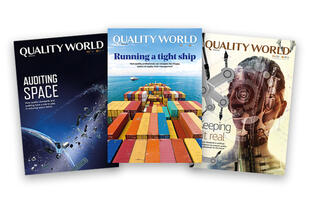
Get the latest news, interviews and features on quality in our industry leading magazine.
The latest from the CQI Podcast
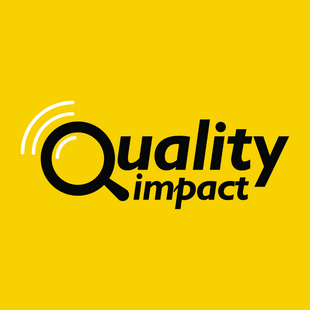
Listen to the Quality Impact podcast, where experts share insights on the evolving role of quality across industries.