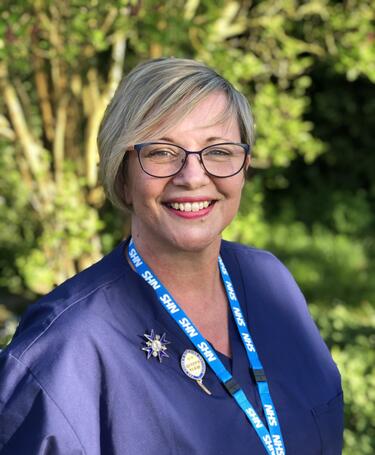
Achieving accreditation as a small company
Su Chantry, Clinical Director at SKC Occupational Health, outlines her journey to ISO 15189 accreditation.
How did you start in occupational health?
My background is nursing. After I left the NHS, I worked for a commercial occupational health business. I built up my experience and my education portfolio and qualified onto Part 3 of the Nursing and Midwifery Council Register five years ago, graduating with a specialist community public health nursing degree in occupational health.
I then set up SKC Occupational Health Consultancy. I am an independent occupational health practitioner offering very specific bespoke workplace health support for small and medium businesses that do not need a big commercial provider.
My fundamental role is workplace health and wellbeing, managing and advising health-related issues in the workplace. This encompasses advising on disability, supporting businesses manage sickness absence, supporting wellbeing and mental health strategies. My Covid-19 swabbing service started as a requirement to support my clients who undertake business and sport-related travel, including Formula 1 crew.
Why did you decide to certify to ISO 15189 Medical laboratories — Requirements for quality and competence?
I wanted to be able to deliver a quality assured Covid-19 testing service. Coronavirus testing was initially exempted as a regulated activity. However, on 15 December 2020, the law changed, and all private coronavirus test providers had to become accredited by UKAS.
Successful accreditation is required to be listed as a UK Government test service and only the listed accredited providers are recognised by UK border authorities – therefore clients are assured that the tests are valid for international travel.
How did you find the process to achieving accreditation?
The process to gaining ISO 15189 accreditation has been quite a challenge as I had no experience of any quality assurance management systems at all. There is an overwhelming level of detail required in the criteria required in the standards, both administration as well as clinical and business/marketing standards. Initially it was confusing, as the Department of Health and Social Care (DHSC) was pushing back to UKAS and vice versa, so initially it did feel as I was going between pillar and post and not getting clear guidance.
The clinical side was quite easy to align with the requirements of the standard. It was really just refining some of the clinical standards and processes. But it became apparent that I needed a quality management system and an organisational approach.
I was really shocked at what sort of resource was involved in meeting some of the accreditation standards. As a single director with no real team, it was quite a challenge. In comparison, a colleague who owns a very large commercial occupational health business has eight members of full-time staff working in his accreditation and audit department.
I needed the support of someone experienced in audit management and quality control and found a colleague, who is an accredited auditor with a particular interest in workplace health management, to help.
There are three stages to the accreditation process. Stage one is the application and collation of a basic level of documentation. Stage two is the development, gathering and collation of the evidence into a framework aligning with the standards, and this needed to be submitted in a tight time frame. Stage three is the assessment.
UKAS were incredibly supportive. They recognised that there were a lot of people needing guidance and started webinar training sessions and then implemented some module training with the support of DHSC. The UKAS-developed webinars were educational and explained the process. Once the assessors had been assigned, UKAS were able to advise and guide in regard to the preparation for stage three.
From my perspective, not being familiar with that sort of process at all, it was quite overwhelming – reading what was required and trying to work out how I was going to continue offering a quality swab service.
How did you view ISO standards before, and are you looking at any others?
I always felt that ISO standards were for very large corporate organisations.
There’s a psychological framework that’s being attached to ISO 45001, for psychological risk management within the workplace. That aligns nicely with occupational health management. That is probably the next accreditation that I would like to achieve, because I still feel that it’s professionally aligned with what I can deliver within my speciality.
Has ISO accreditation improved or changed your business?
It’s something I’m hugely proud of achieving with the support of my quality manager. It gives me a sense of pride as a small independent business to be able to reach a standard that takes a huge amount of time and commitment.
I’ve always taken my quality of service delivery and professionalism with utmost seriousness. What it means now is that I can market and evidence that with the standards that I’ve achieved. My website has been updated to reflect this and I’m taking marketing more seriously. I’ve set up a process that formalises requests for feedback and am now on Google Business. I would never have done that without the quality standard.
It’s definitely helped improve my business focus and model. If you’ve got an accreditation such as an ISO, I do feel that’s recognised in the business context more than clinical standards.
You managed to achieve this accreditation during the Covid-19 pandemic. How did the pandemic change occupational health for you?
On a clinical level, it was very challenging. We had to pull back from the health surveillance element of our role completely because there was no face-to-face clinical contact. We have had to review some of our practices. For example, with respiratory management, do we need to be having everybody coming in to do lung function tests when we can have a robust risk management approach with a good screening questionnaire?
The Stage 3 assessment is a full day, and it was very nerve inducing. Because it was done remotely it did mean that we could book in times very easily. They were able to assess my clinical work through the virtual process, and I felt that was probably less intense, rather than someone sitting there watching with a clipboard.
In terms of my clinical delivery for Covid-19 swabbing, I’ve been able to offer a remote service of self-testing under guidance. Clients book a half an hour video call and I supervise virtually.
What advice would you give to other occupational health companies who are looking to become ISO accredited?
Believe that you can do it; follow the process, don’t challenge it; and make sure you get the right people around you to help you through. But don’t underestimate how much hard work it is, because it’s quite overwhelming.
You have to have a framework that you can work to. When I started, I thought, “Oh, it’s a bit of a tick-box exercise and, yes, I can do that.” Then my colleague came on board and aligned it at a level that I would never ever have been able to achieve on my own.
You also have to be focused on how the standard applies to the services you’re offering. You have to have a rationale as to why you’re achieving that accreditation.