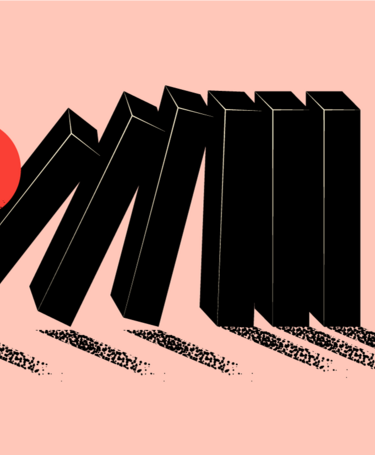
Embracing failure as a quality professional
Progress indicator
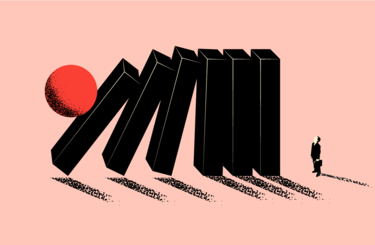
Kevin Newey CQP MCQI, Head of Quality at Graphcore, explains why quality professionals should embrace failure rather than fear it.
Quality and assurance professionals spend much of their time dedicated to improving the success of organisations, often by ensuring things are done the ‘right’ way. However, standardisation comes with a risk of limiting innovation and, if applied without care for context, can also foster a ‘tick box’ approach to quality management.
Back in 2021, in the depths of one of the Covid-19 lockdowns in the UK and looking for something different to occupy my time, I decided to enrol in an online clowning class. Part of the clowning craft is learning to do things deliberately incorrectly. How many ways can you incorrectly put on a coat? Are any of them funny? It was as uncomfortable as it was illuminating. It is my belief that Quality 4.0 requires us to embrace the discomfort of failure in a similar fashion.
Getting things wrong
In today's complex and rapidly changing environment, it is more important than ever for organisations to get on board with the concept of getting things wrong. This is driven by the prevalence of volatility, uncertainty, complexity, and ambiguity (VUCA) in the modern organisational landscape, as cited by Bob Johansen in his 2007 book Get There Early: Sensing the Future to Compete in the Present.
In this environment, organisations that are unwilling to adopt a growth mindset and embrace failure will struggle to adapt and innovate in the face of constant change, as noted by Carol Dweck in Mindset.
In his book Quality is Free, Philip B Crosby says: "The best mistake is the one from which we learn the most. To learn from a mistake, we must first admit it. Then we can analyse it and take steps to prevent it from happening again."
“Quality professionals are often focused on the dogma of total defect or failure prevention. ‘Zero defects’ is a laudable vision, but across the entire range of characteristics of a product or service it is a statistical impossibility; or to put it another way, there is a risk that failures will happen.”
This should be bread and butter to quality organisations, but is surprisingly uncommon and requires management buy-in, a structured but flexible problem-solving methodology and a high degree of psychological safety.
However, even more challenging to adopt are deliberate acts of failure. Quality professionals are often focused on the dogma of total defect or failure prevention. ‘Zero defects’ is a laudable vision, but across the entire range of characteristics of a product or service it is a statistical impossibility; or to put it another way, there is a risk that failures will happen. Accepting that defects will happen means they can be consciously managed and leveraged to an organisation’s advantage.
We should – and must – strive to improve the quality of our goods and services through improving our processes, systems and people. The recent pandemic and global instability have made many people realise that it is a fallacy to think that we can control all outcomes 100% of the time.
Organisational design
To make sense of this complexity, David Garvin proposed Eight Dimensions of Quality. These are: performance, features, reliability, conformance, durability, serviceability, aesthetics, and perceived quality. The organisation may choose to prioritise some at the expense of others at any one moment, and some dimensions may be mutually exclusive. For example, mobile phone manufacturers tend to prioritise features and aesthetics over reliability, durability and serviceability. Garvin quotes a chair of Cray Research as saying: “If a supercomputer doesn’t fail every month or so, it probably wasn’t built for maximum speed.”
This type of approach requires intentional organisational design, thoughtful product architecture and a deep understanding of customers and context – a laser focus on what is critical to quality. This could work practically by implementing different levels of control in various parts of the organisation depending on their unique context within the organisation; for instance, financial processes are likely to require tighter controls than research and development.
Netflix’s Chaos Monkey software regularly takes random servers out of action. These are live, customer-facing servers, not test environments. When the inevitable happens and servers go out of action unexpectedly, engineers have already designed in redundancy so the failure is invisible to the customer.
Traditional business continuity methodology requires organisations to be resilient to disruption. However, the concept of antifragility, as outlined by Nassim Nicholas Taleb in Anti-fragile: Things That Gain from Disorder, challenges quality professionals to design organisations that are not only resilient to disruption but grow stronger and thrive in disruptive contexts. Experimenting with deliberate failure is one way to do this.
Tightly controlled, top-down organisations, where failure is punished, will stifle the innovation organisations need to thrive in a VUCA backdrop. Empower teams to experiment, break stuff and rebuild stronger. Context is everything though; how this is implemented in a medical devices business for example, would be very different to a less regulated environment. The trend of increasing regulation needs to be met with thoughtful quality practice, not anarchy.
Learning and improvement opportunities
In conclusion, the importance of getting things wrong cannot be overstated in today's complex and rapidly changing global environment. To remain relevant, quality professionals need to shed the image of policing ‘doing things right’ and focus on how to ‘do the right things – fast!’.
Rather than striving for perfection, organisations should embrace failure as a learning opportunity and proactively as a key component of their strategic planning and decision-making processes. By doing so, they can drive continuous improvement, make breakthrough change that their customers and stakeholders care about and, ultimately, position themselves for long-term sustainable success in an uncertain world.
The CQI publishes special reports and resources for members. Download yours for free.
Find a quality course
Search our database of global training partners for a certified quality training course in a location near you.
Quality World
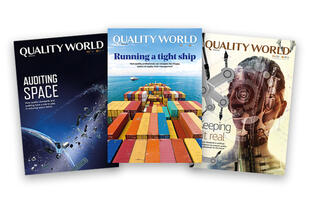
Get the latest news, interviews and features on quality in our industry leading magazine.