Search
Search our content by date or relevance.
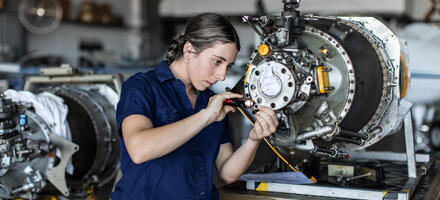
The CQI welcomes GKN Aerospace as a corporate partner
We are delighted to welcome GKN Aerospace to our expanding corporate partnership programme, with access to a global network of quality experts and innovative resources and tools.
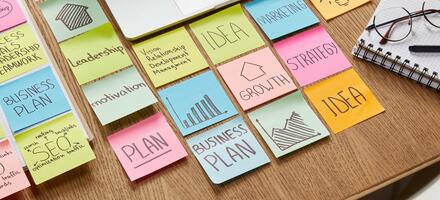
The power of benchmarking
Andrew Ward CQP MCQI outlines benchmarking as a business improvement tool, outlining the benefits and the potential pitfalls.
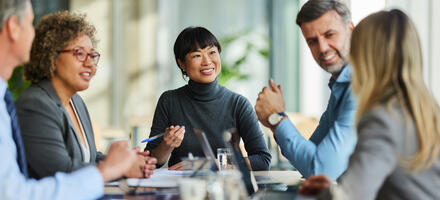
Unlocking value through quality management excellence
Mike Turner, Head of Research Innovation, CQI, shares early insights and discoveries from the CQI's initial phase of research with Cranfield University, focusing on the value of quality management.
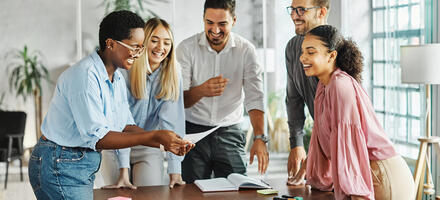
Think differently: a journey of innovation and continuous improvement
Contributing to our World Quality Week 2025 blog series, Mitch Reed CQP MCQI, Continuous Improvement Specialist, Olympus UK & Ireland, explores how organisations overcome setbacks by embracing new ways of thinking.
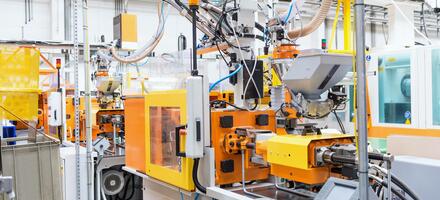
3D metrology in moulded components
Moulded component manufacture presents several challenges for quality professionals because of component types, manufacturing techniques and base materials. Derek Scott CQP FCQI argues that contactless 3D measurement is a superior strategy for industrial engineers working in this field.
Chartered Quality Institute AGM 2025
The Annual General Meeting will take place digitally to encourage and include our international members.
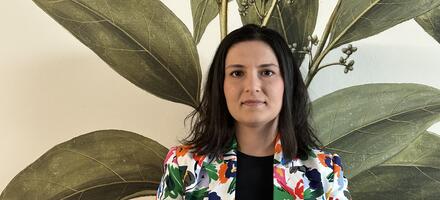
Auditing: it's good to go global
Gulsah Tekatli recently became an IRCA Associate Auditor and here she shares her journey into quality in Turkiye and her current home in Hungary.
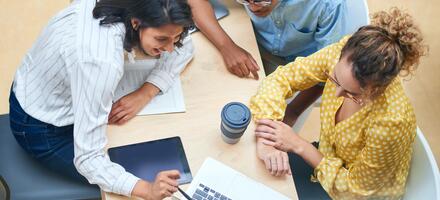
Through the lens of the auditee
(Ben) Ho Bun Chan CQP MCQI offers audit insight from the other side of the table, examining how an organisation undergoing ISO certification for the first time can get the best out of the process.
Building a programme of events to support your professional development
Throughout 2025, we'll be adding virtual and in-person events that satisfy your professional needs.
Visit this Events Calendar regular for updates.
Building a programme of events to support your professional development
Throughout 2025, we'll be adding virtual and in-person events that satisfy your professional needs.
Visit this Events Calendar regular for updates.